While not strictly part of “The Project” build, I thought this might be interesting to document.
Having purchased a pair of 4L2 pipes for the Project, and fitted them to my runaround LC to cure the paint, I was left staring at the 31k pipes I had removed.
Alongside the 1UA pipes from the donor bike, they had the rustiest downpipes I had ever seen!
Is it the seaside air? An excess of salt on the roads in winter?
both my bike, and the donor bike are/were ridden throughout the summer and winter months.
Do all Elsie pipes suffer this way?
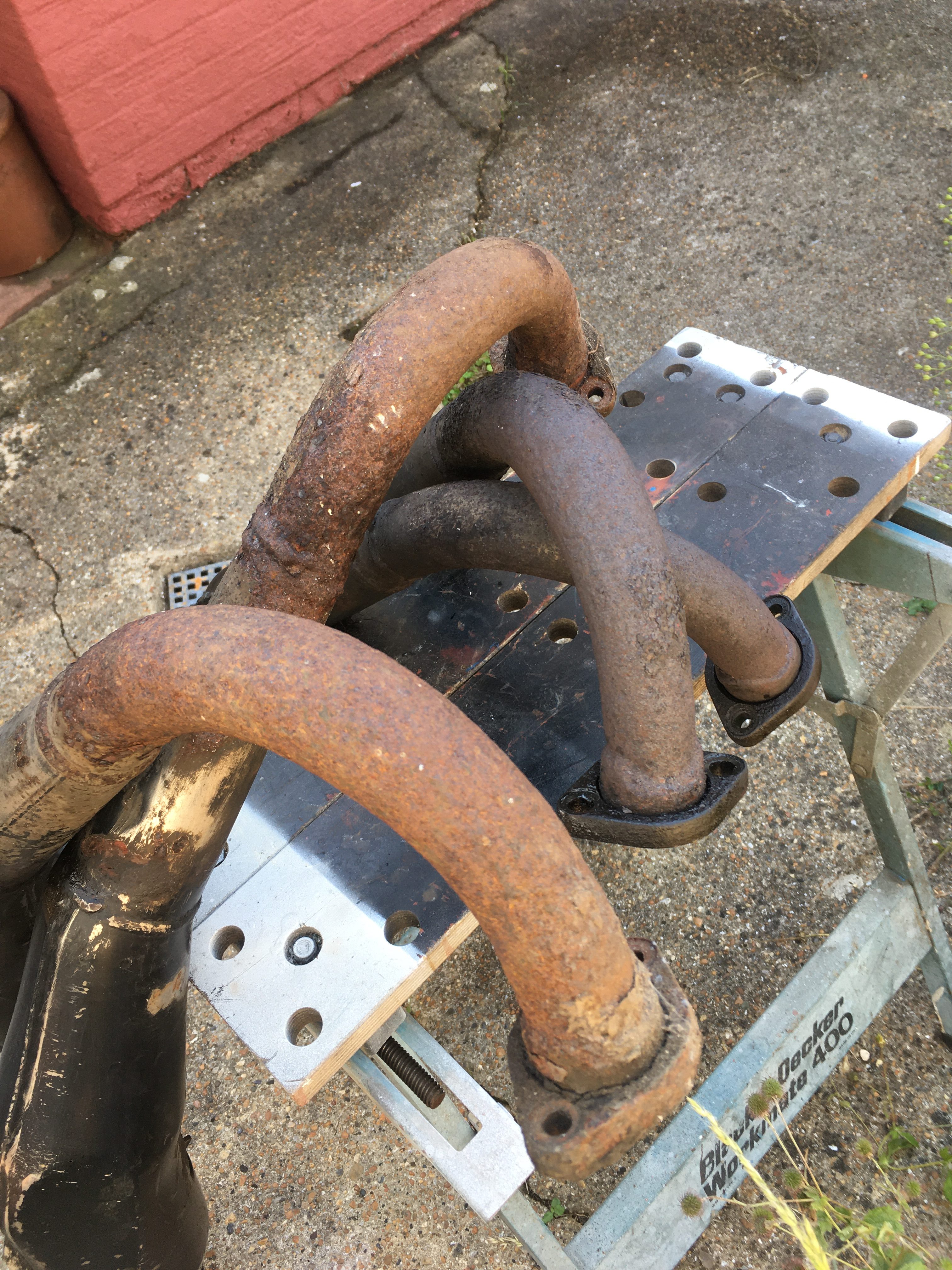
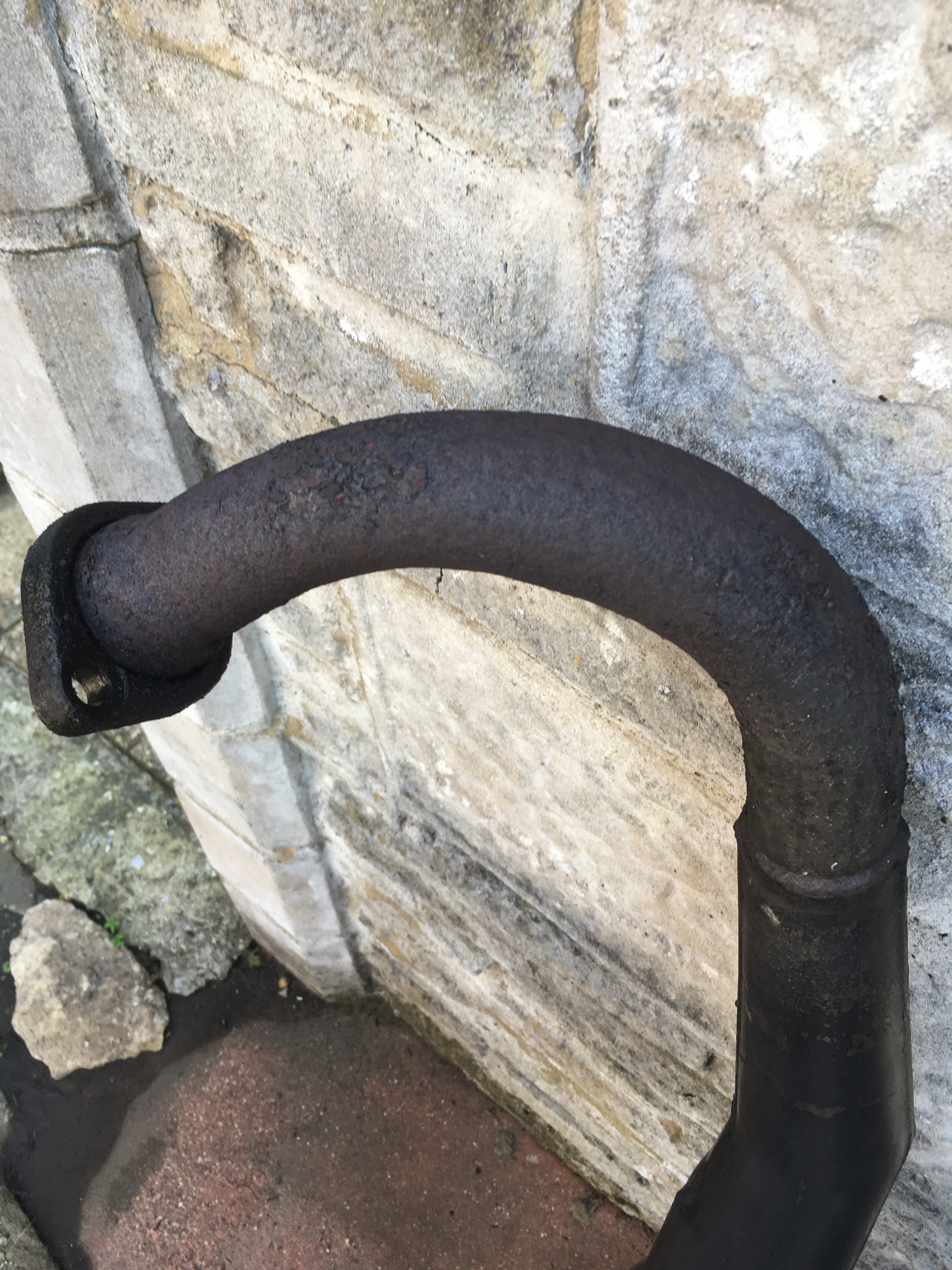
What is to be done?
I don’t want to put the 31k pipes directly back onto my bike in this state, and the 1UA pipes will either be sold or used in the future.
First step is to remove the loose rust and see what the damage is. My puny rotary wire brush on the drill seemed inadequate for this job, so I invested in an upgrade.
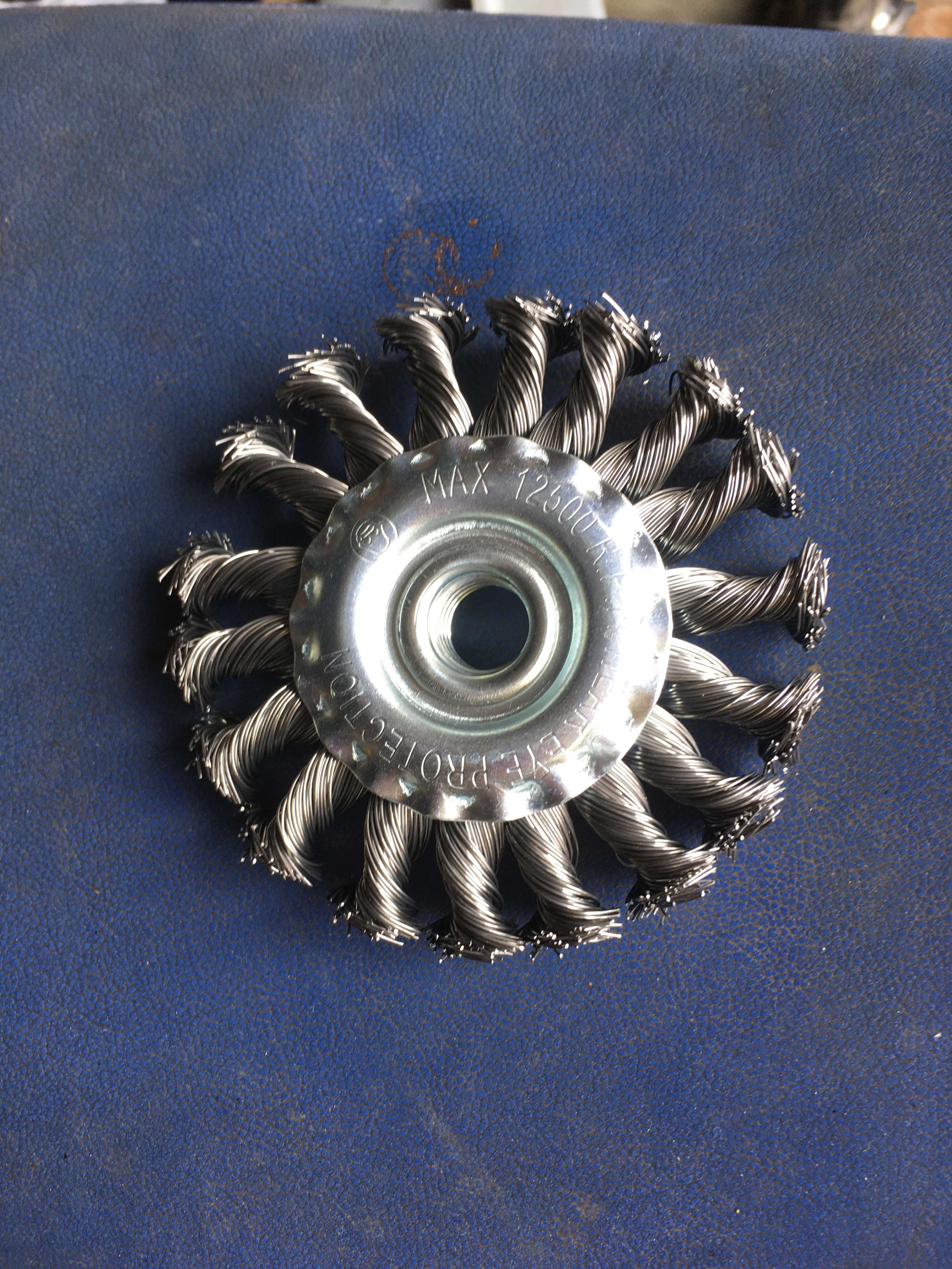
This doesn’t get fitted to an electric drill, but to an angle grinder!
It made short work of the rust on the first pair of downpipes tackled, the 31K pipes.
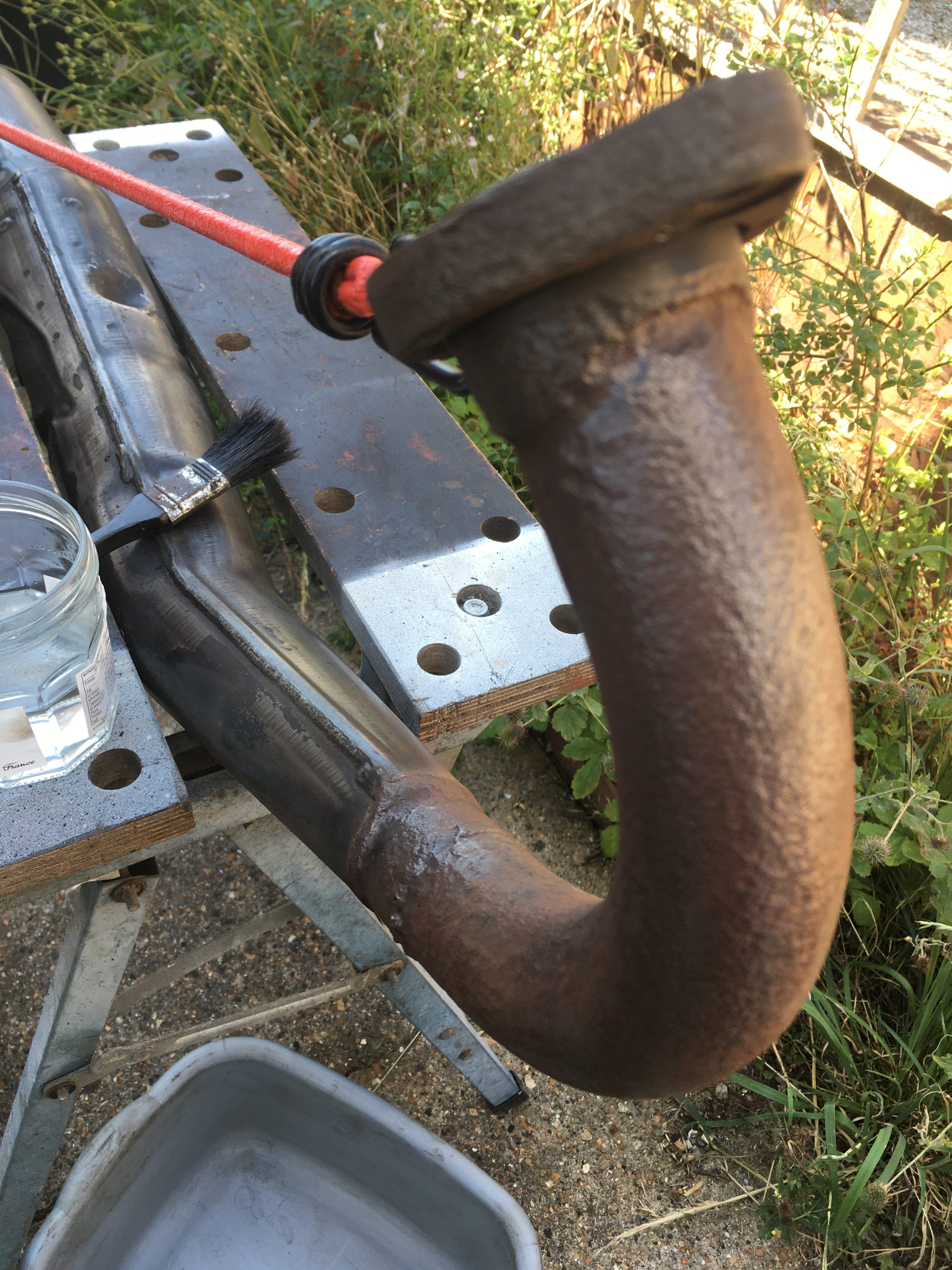
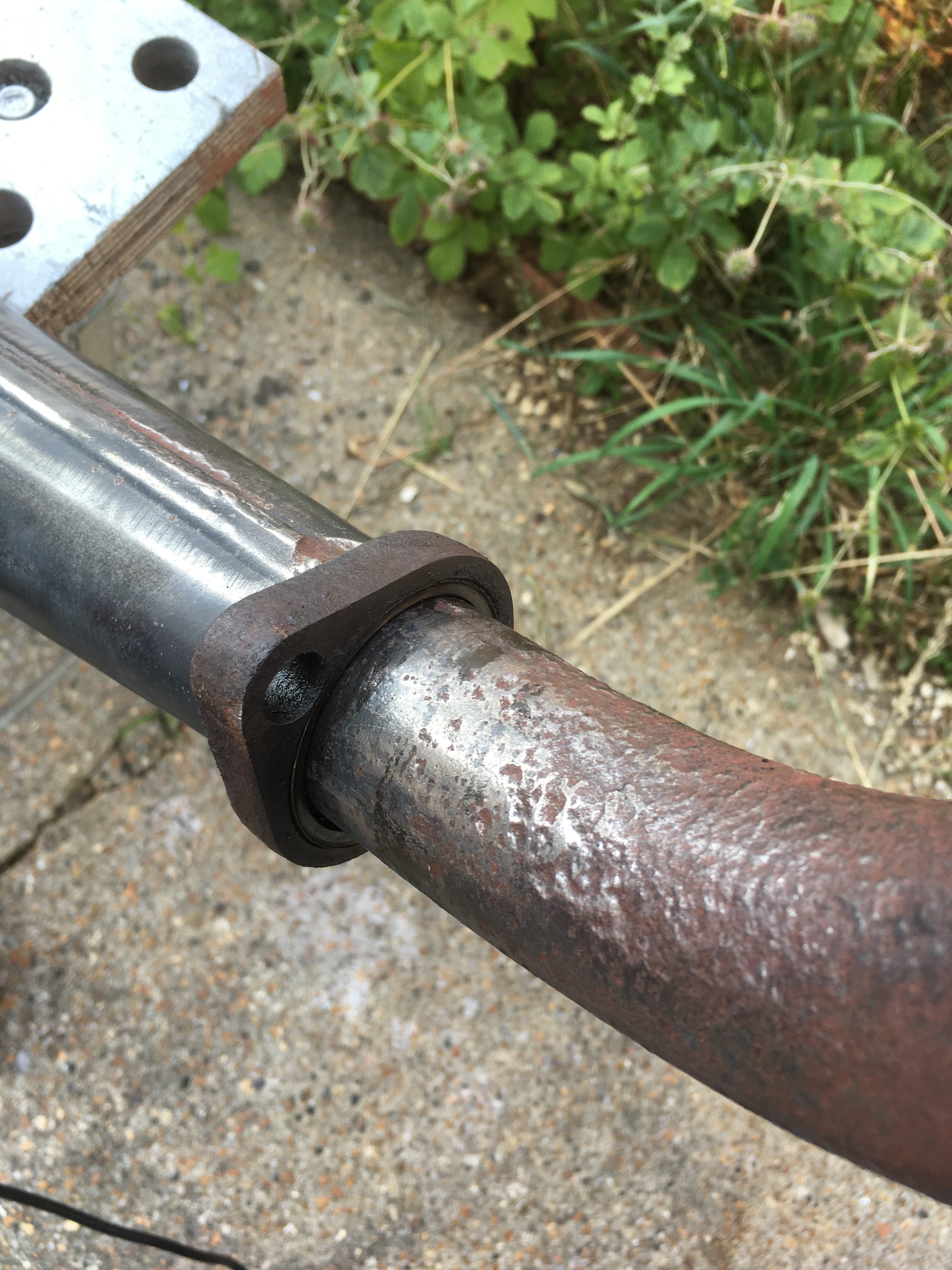
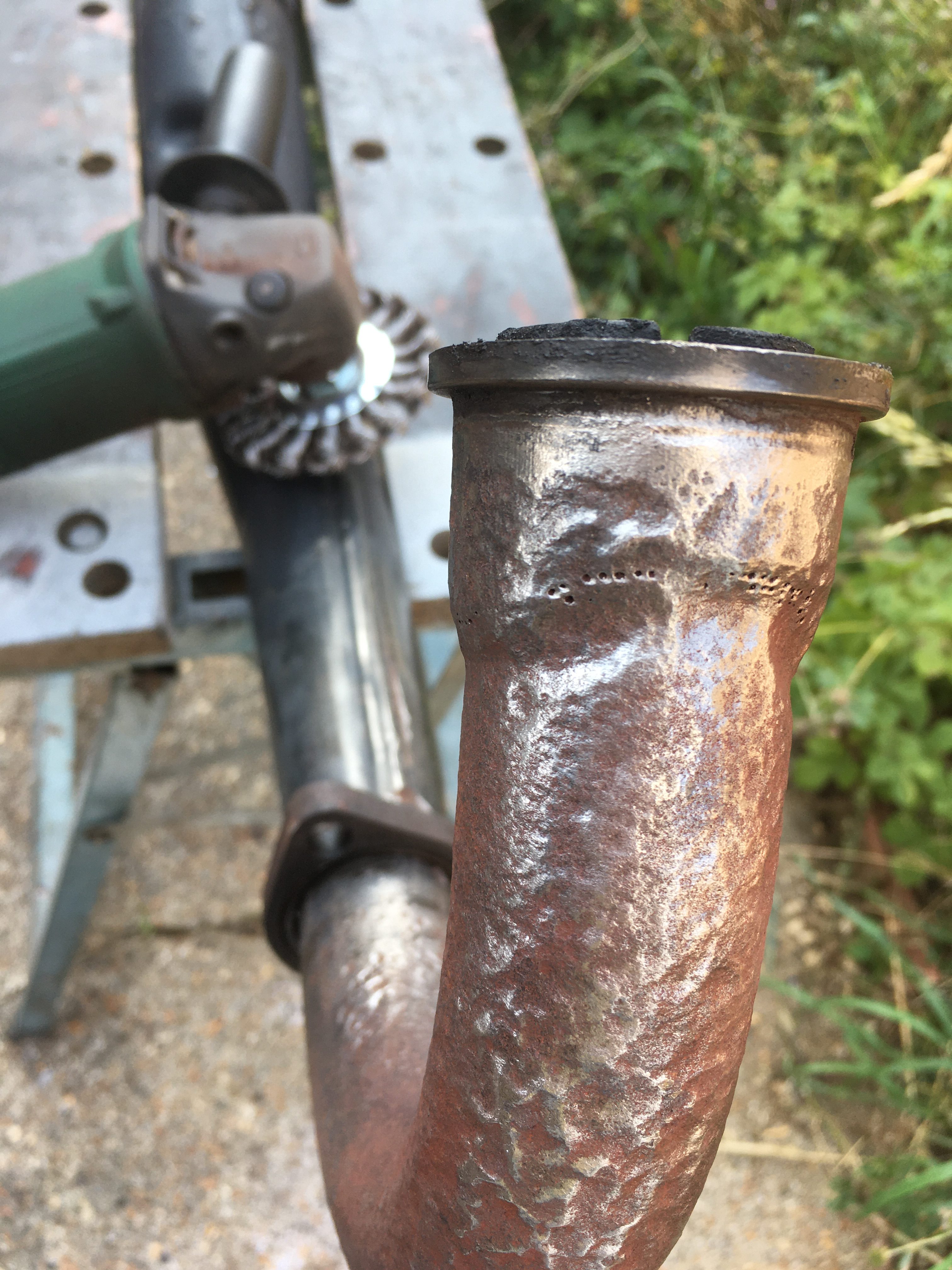
Even with the new wire brush, it is clear that I cant remove all of the rust and get back to bare steel. the corrosion has caused some deep depressions, and an undulating surface. On the left hand pipe, there are some holes which go straight through into the inside of the pipe.
I should probably weld up the holes at least, but I wanted to try something else, which would work both for the holes, (while they are still pinholes), and for the depressions and undulations, so I looked up “High Temperature Filler” and came up with only one product which it seemed could hope to deal with the temperatures at a 2-stroke’s header pipe.
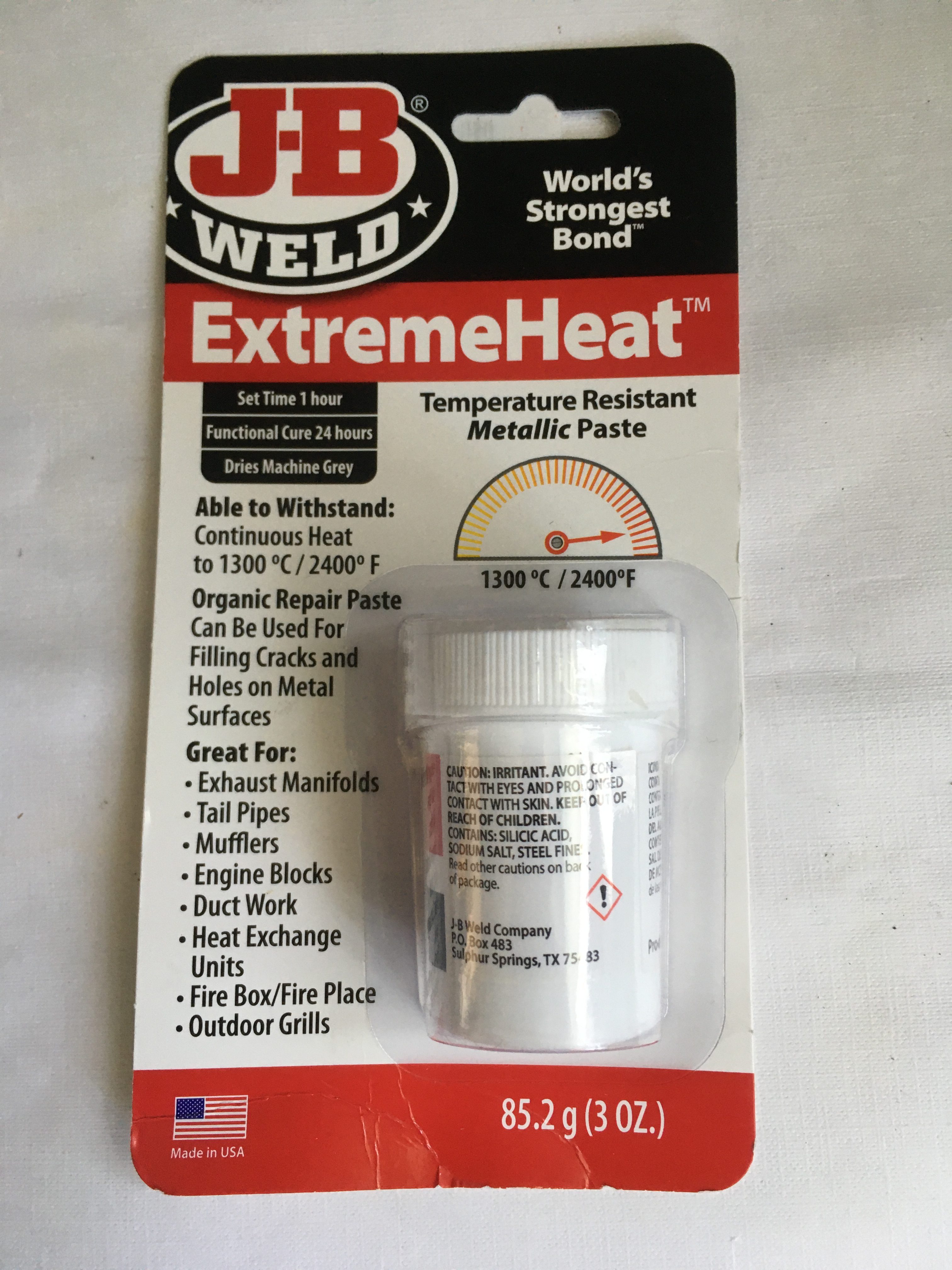
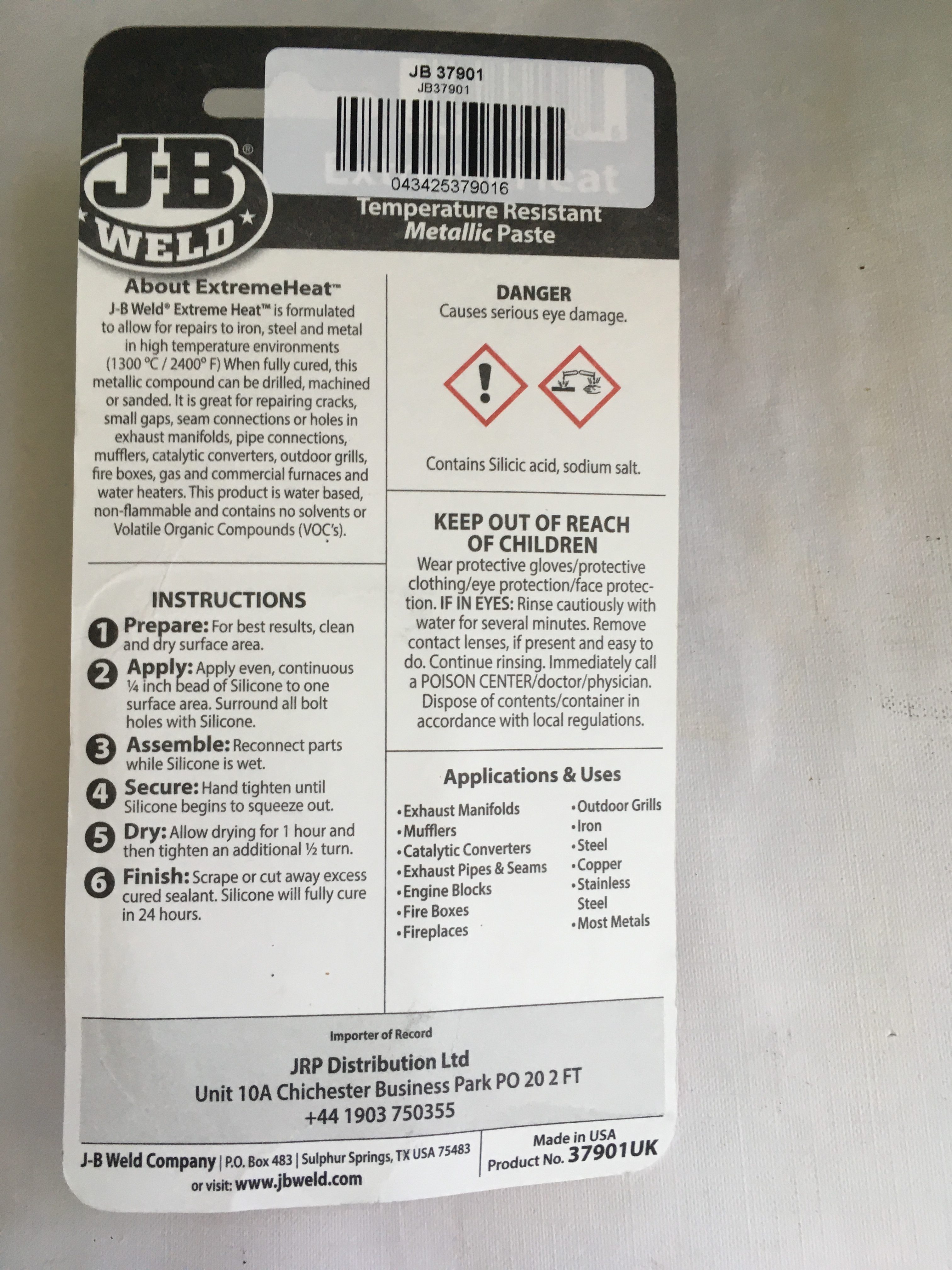
JB weld extreme heat filler comes in a small tub at a large cost.
My immediate thoughts are that the product does not fill me with confidence. the instructions on the back seem to be for another product entirely, however we’ll give it a go.
As i understand it, the contents of the tub are a one time use product, so once it’s open, i should be ready with all my use-cases… all 4 pipes with rusty/corroded downpipes will be prepared.
I’d like to be able not only to stop up the holes and fill the big corrosion depressions, but to surface the undulations so that the pipe looks whole again.
Perhaps the JB-Weld won’t rust, even though it says it contains “iron fines”.
The surfaces are to be clean and rust free, so the next step is to reduce the surface rust on the downpipes.
I’ll do this once again with phosphoric acid, painting it on with a paintbrush in the hope that it converts enough of the iron oxide to ferric phosphate that any repairs and paint laid on top will be on a sound substrate.
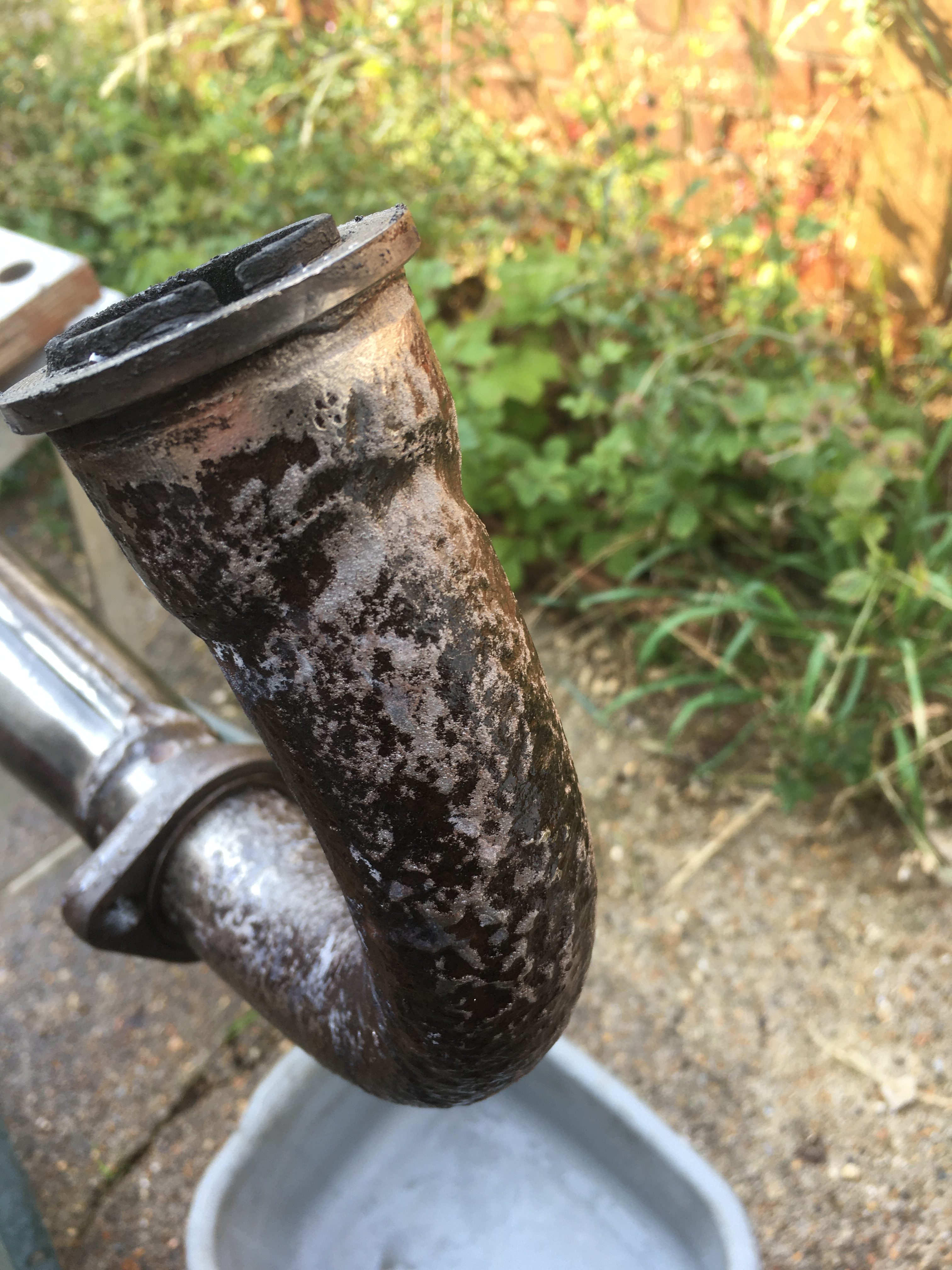
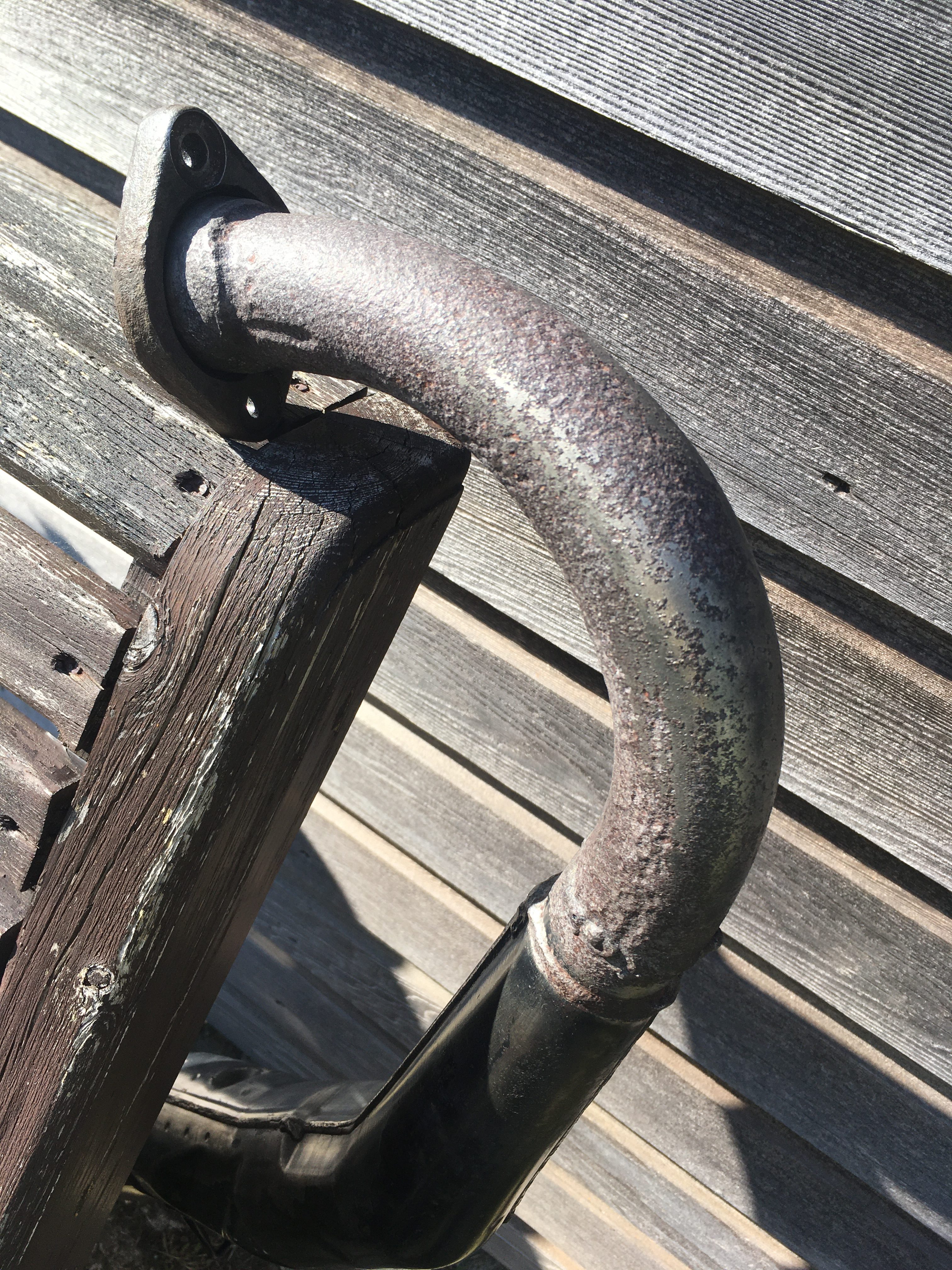
The RHS pipe in the photos above has been wire brushed, and treated with painted on phosphoric acid twice. there are still notable rust deposits deep in the pits, so I will need to go again… and again, until the contents of the pits remain black after wire brushing.
The Left hand pipe shows what 15 minutes of Phosphoric acid does before it is rinsed with lots of water, and wire brushed again. (Note the plastic tub under the pipe to catch the acid runoff so I don’t track it into the house on my shoes).
the rust has turned black… i.e. it has been converted to Ferric Phosphate, but I know that when I wire brush it again, there will be rust underneath.
Ideally, I would submerge the pipes into an acid bath, but i don’t have unlimited quantities of phosphoric acid. the painting on seems to work well.
I need to get to a state where the pipes are showing no red iron oxide after the final wire brushing step of a treatment cycle.
The corrosion damage to the pipes is clearly visible now.
This could be a long road, before I get to apply the JB Weld.
The 2 31k pipes half done… the 2 1UA pipes still to go.
After a few rounds of treatment, I decided that life is too short.
The Phosphoric acid creates the black Ferric Phosphate on top of the rust. The rust therefore no longer reacts with the acid. Scrape the coating off with a wire brush to re-expose the rust, and start all over again.
This could take hundreds of cycles!
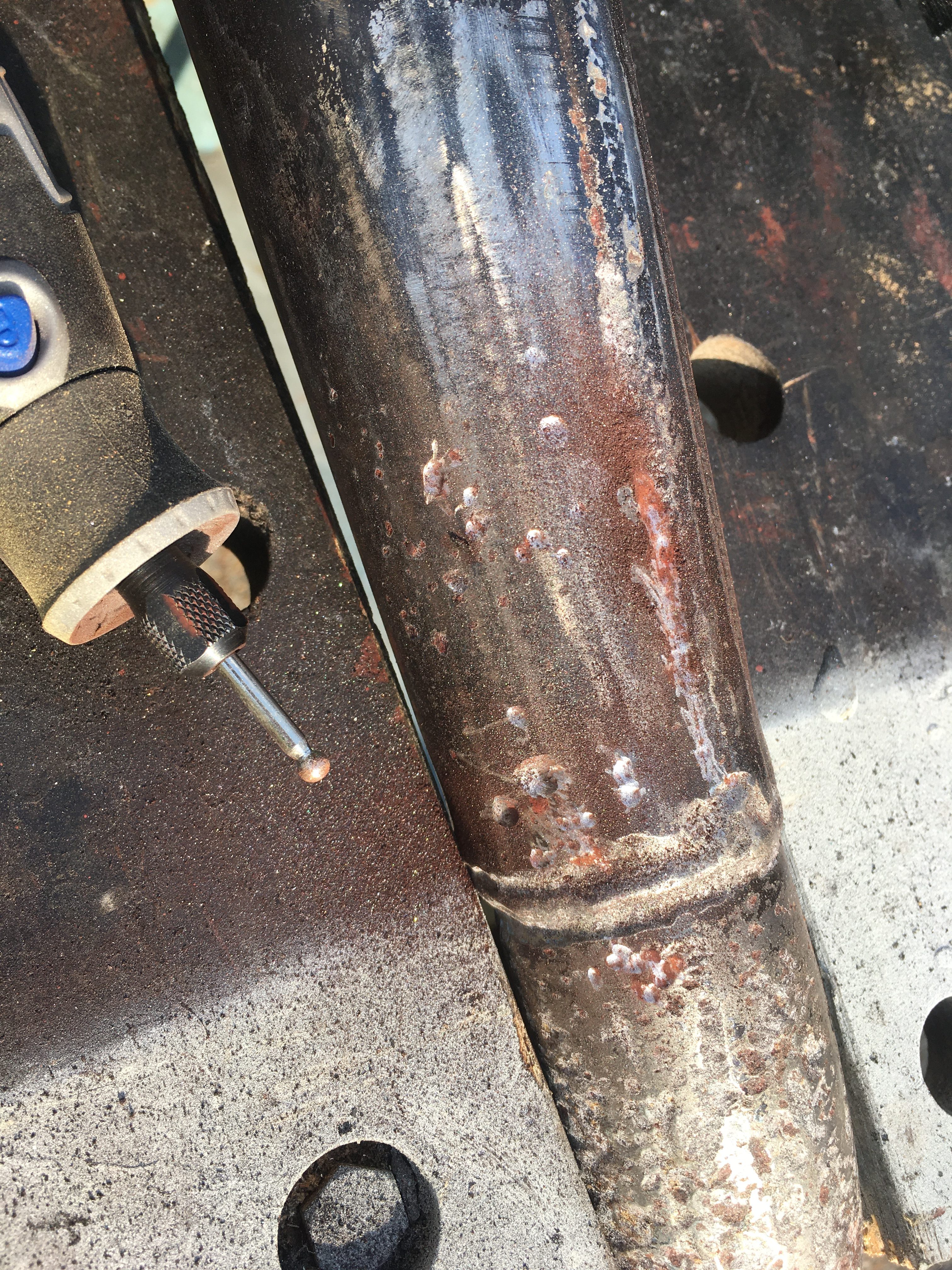
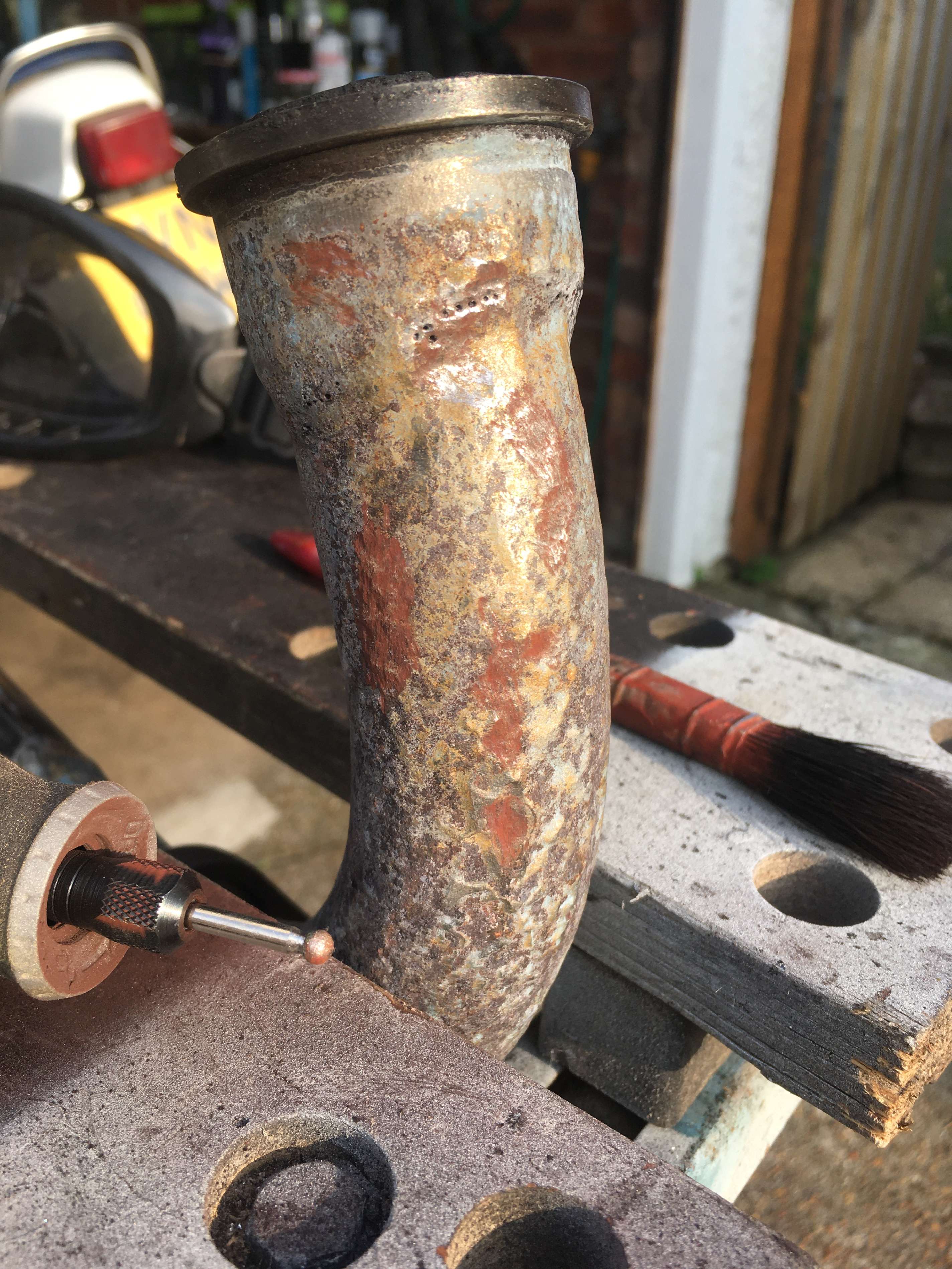
I decided on a new strategy.
There were clearly some deep and holed areas on the headers. i would prioritise them and grind them back to shiny metal with a Dremmel. then fill with the JB weld.
Any JB weld left over, I’d just slather on top of the black areas and monitor over the next few months to see if that is effective.
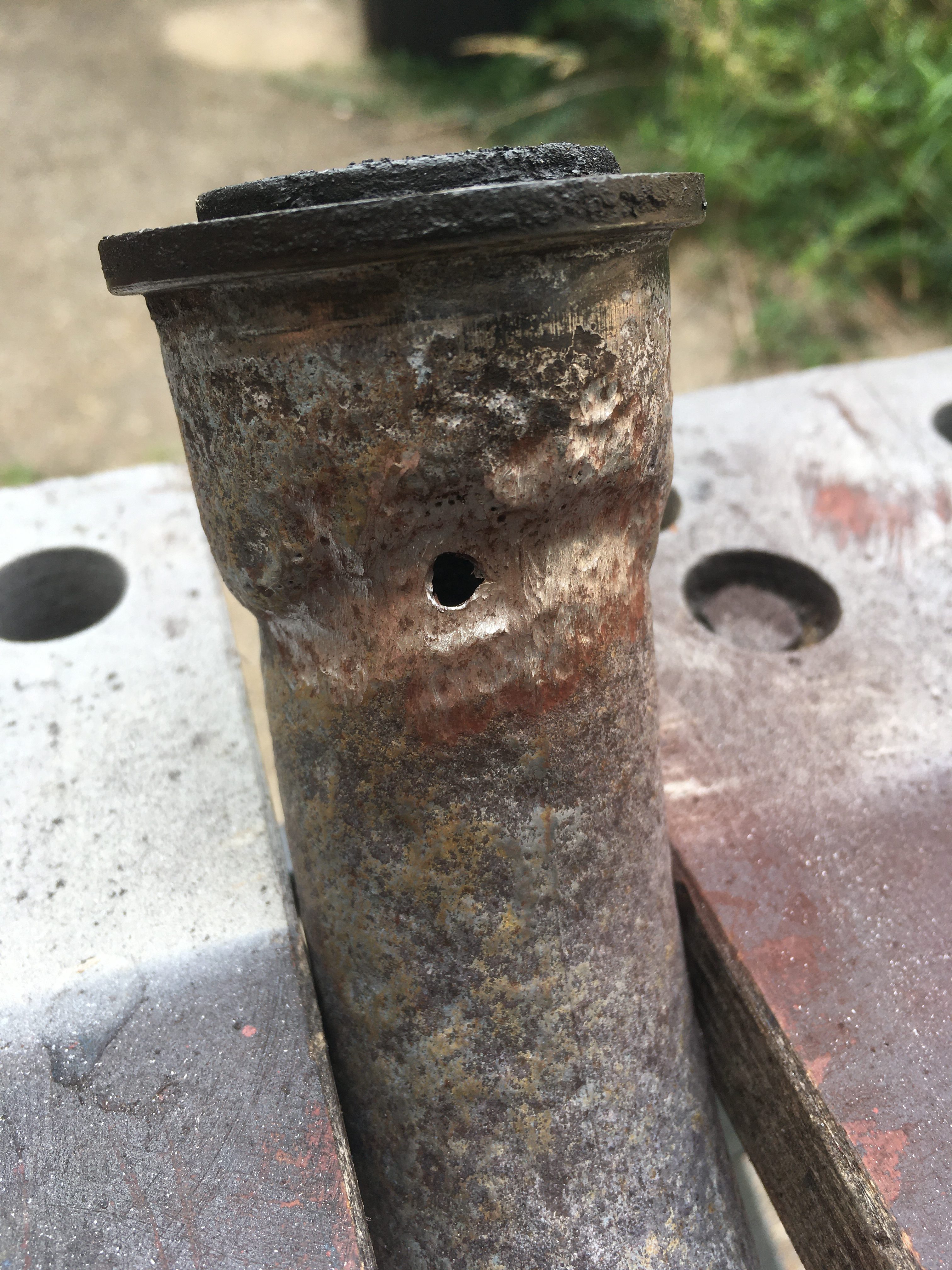
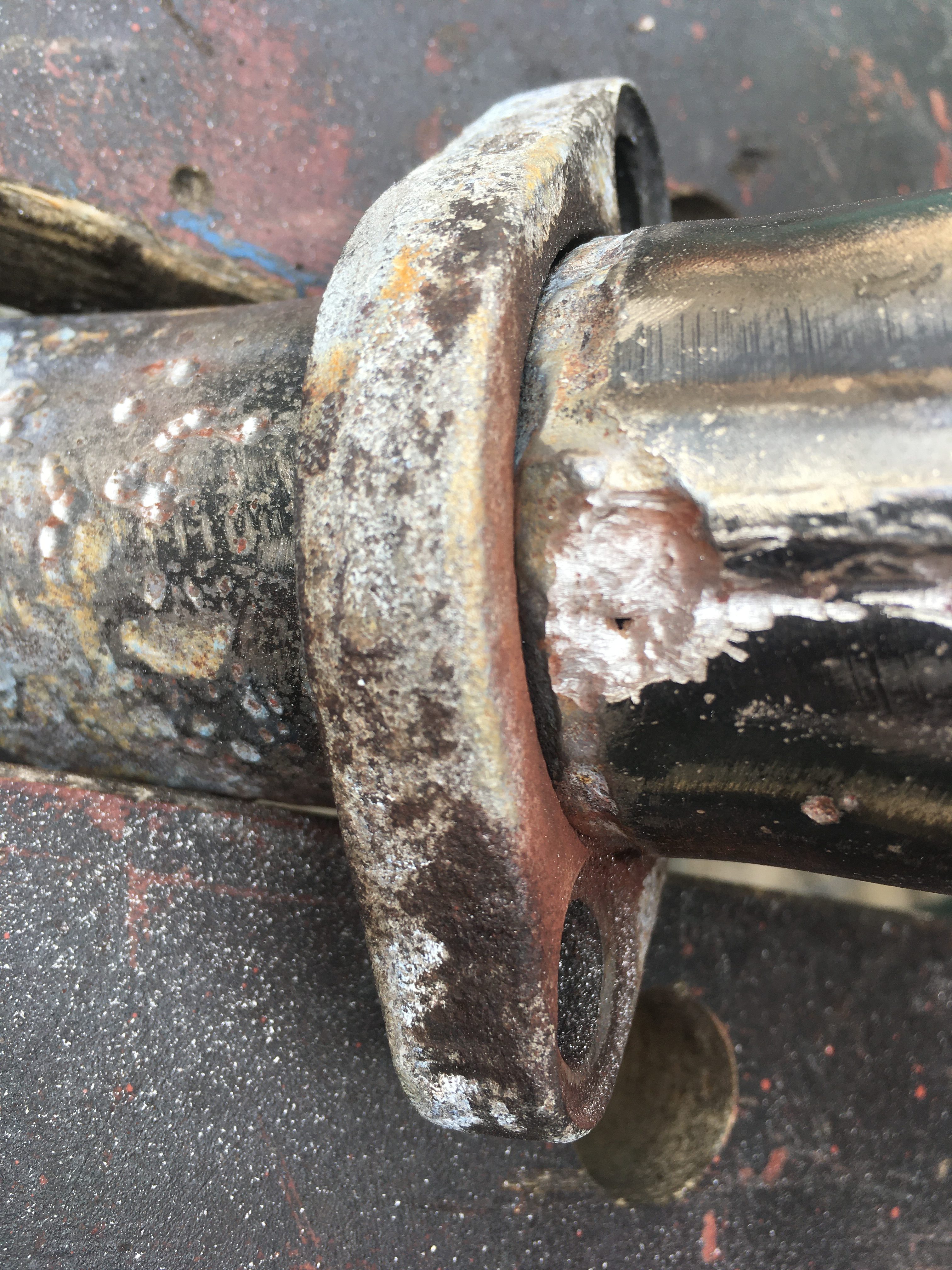
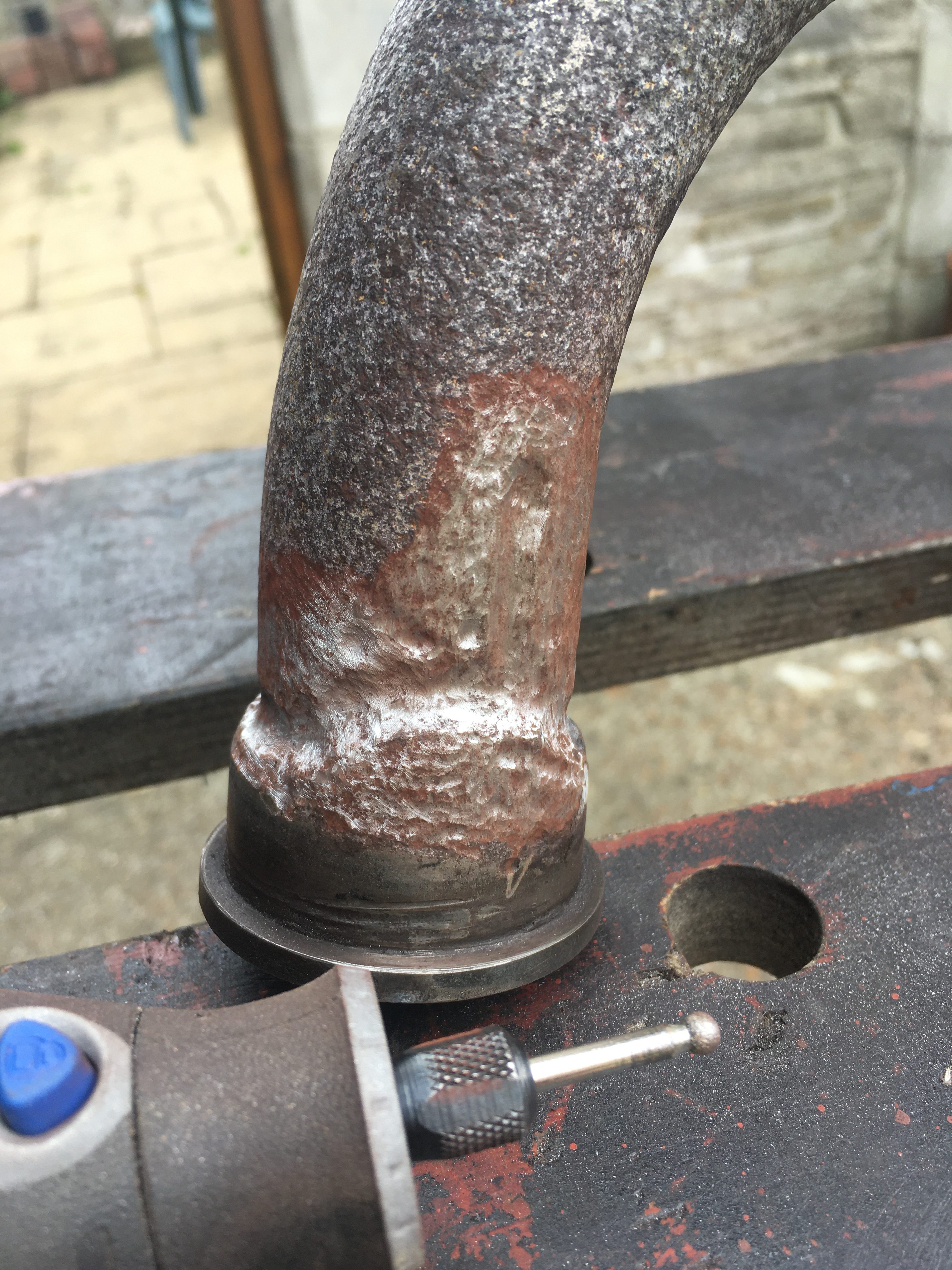
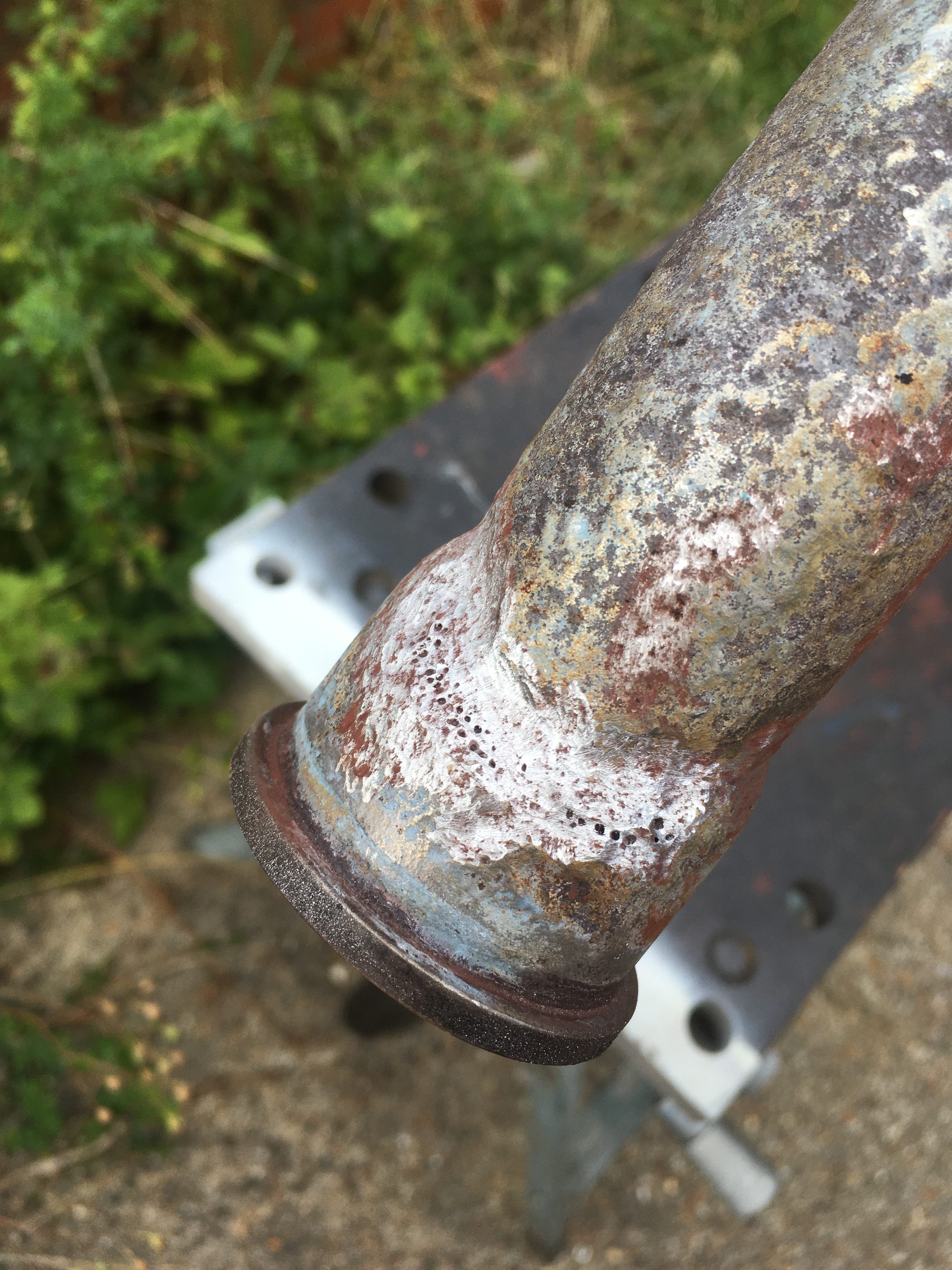
The JB weld comes in a small 3oz tub, which to me seemed a little stingy.
In fact, this is about all you can use before the filler gets too “tacky” to use, and just falls off of the surface you are trying to fill.
Once the grinding was done to the limit of my ability to maintain concentration on the task, I opened the pot of JB weld, removed the airtight seal, and gave it a stir, before wiping it around the affected areas.
There was plenty to cover the dremmeled areas, and most of the worst corroded areas of both the 31k downtubes.
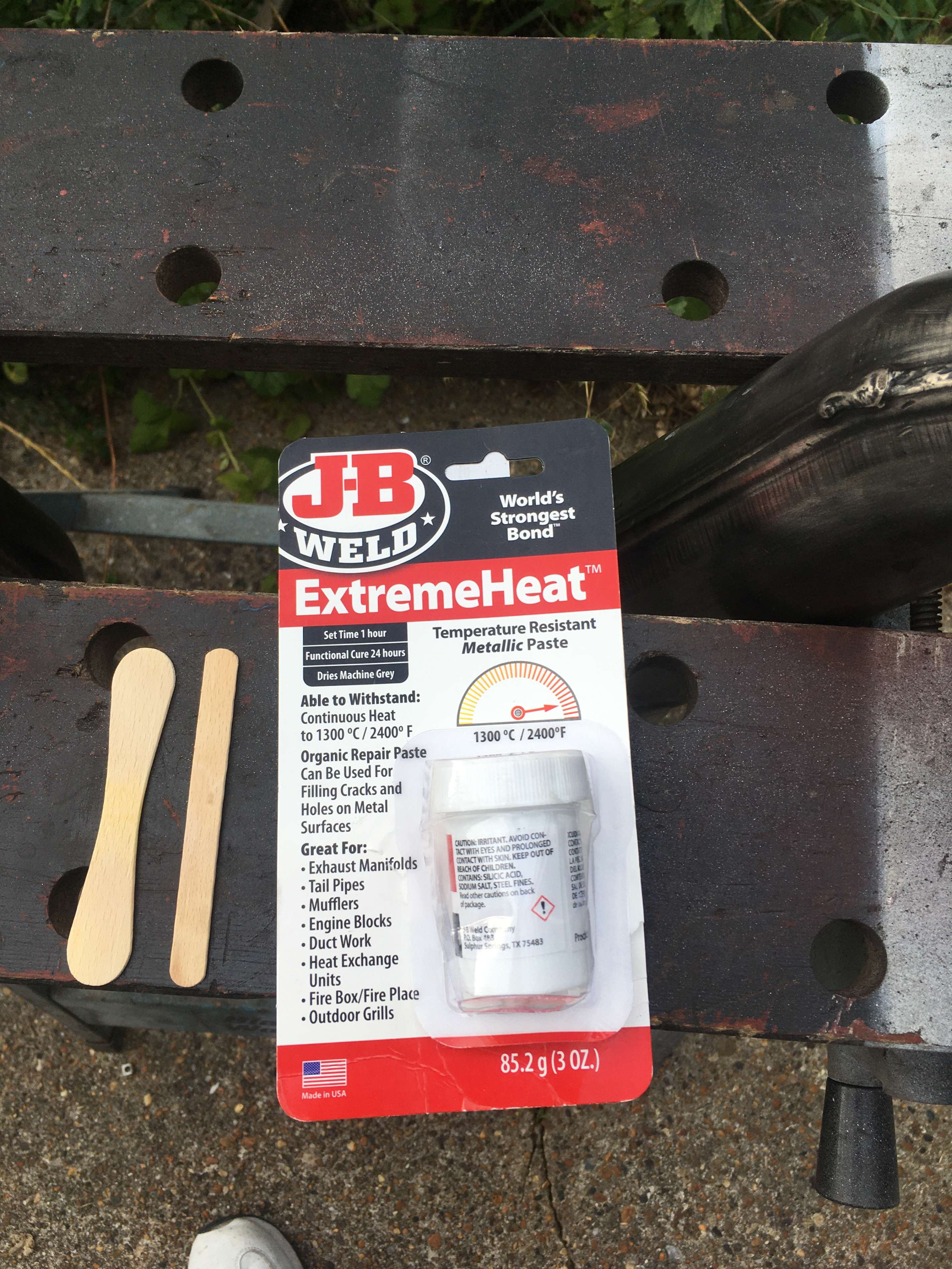
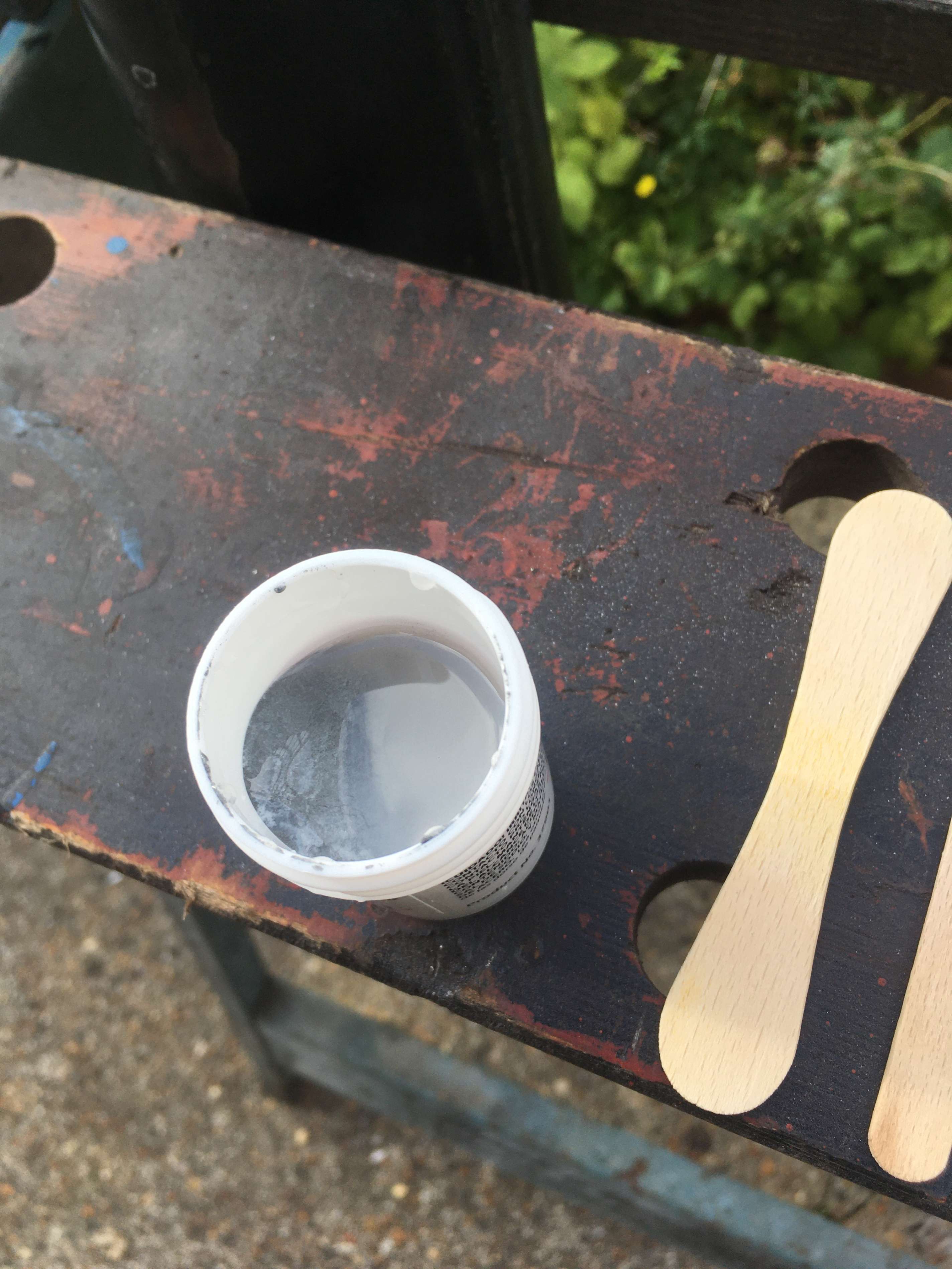

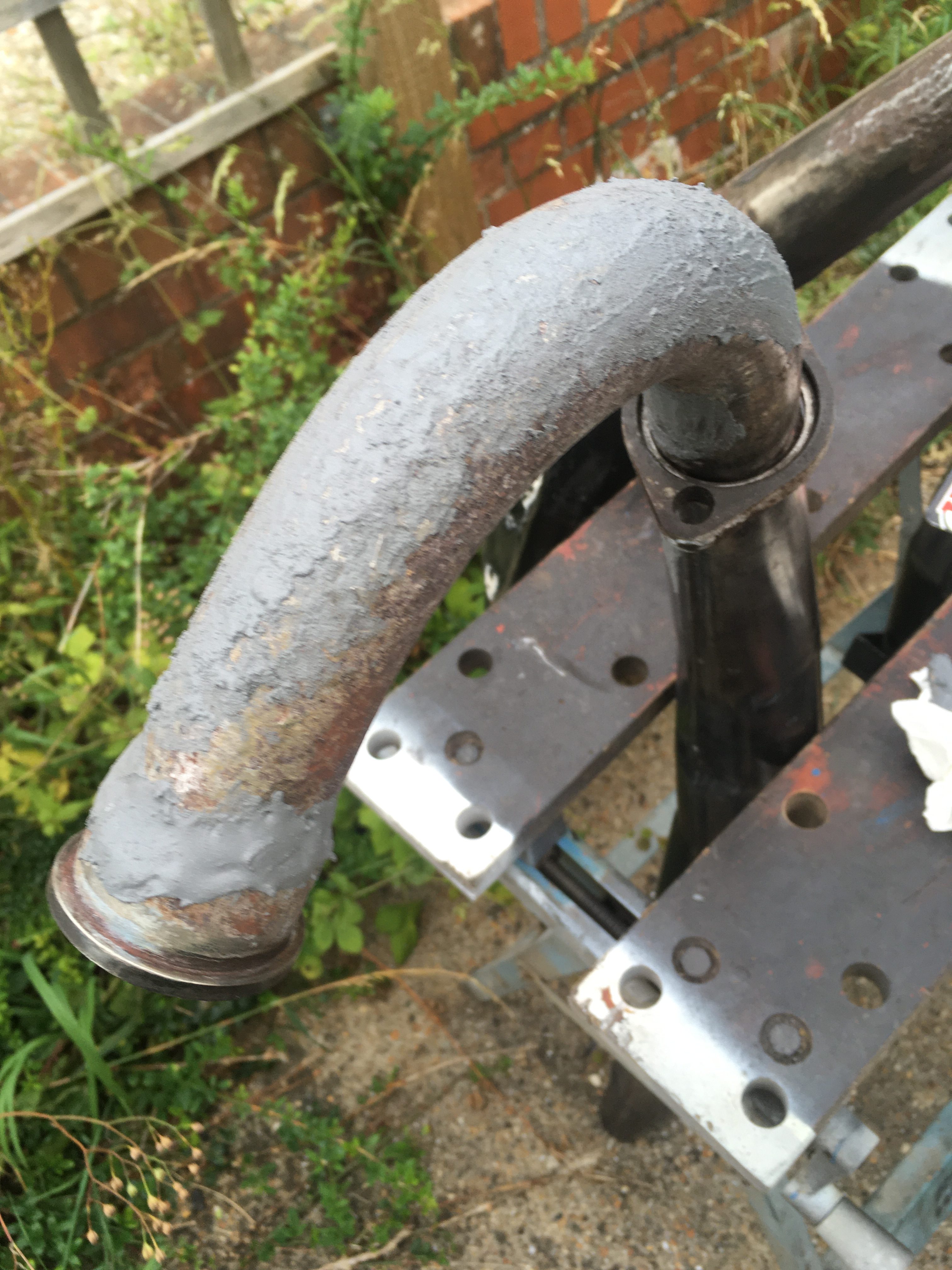
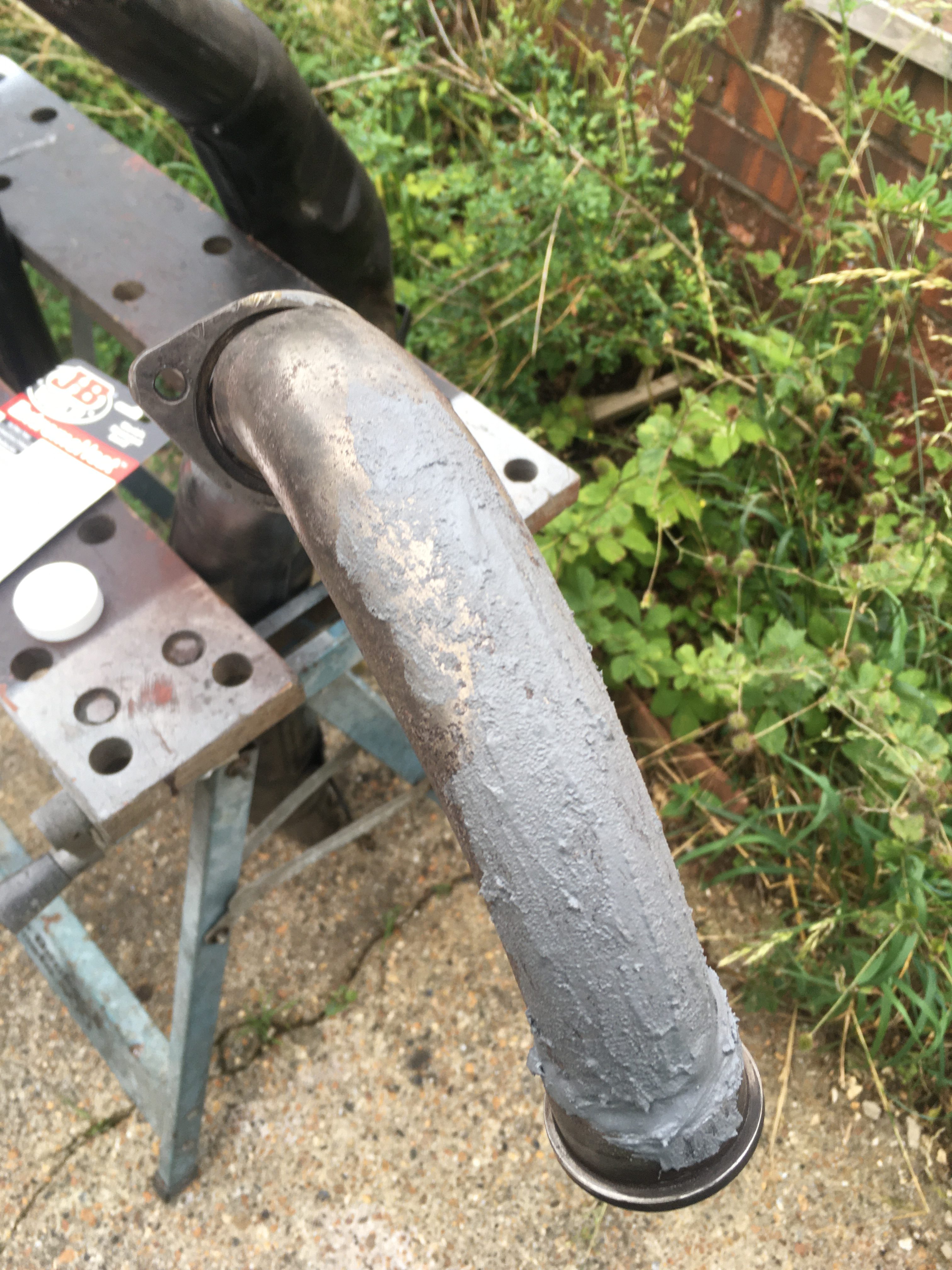
There was about a quarter of the pot left once I had finished, and it was rapidly going off, so I dragged out one of the 1UA pipes I had merely wire brushed, and used the rest of the paste quickly before it hardened completely. this is just an experiment to use up all of the paste.
These pair of 1UA pipes are so badly damaged I was going to take them straight down to the recycling center, (what we used to call “The Dump” in less enlightened times 🙂 )
If the JB weld proves effective, it may be possible to reclaim them at the cost of another couple of 3 oz. tubs.
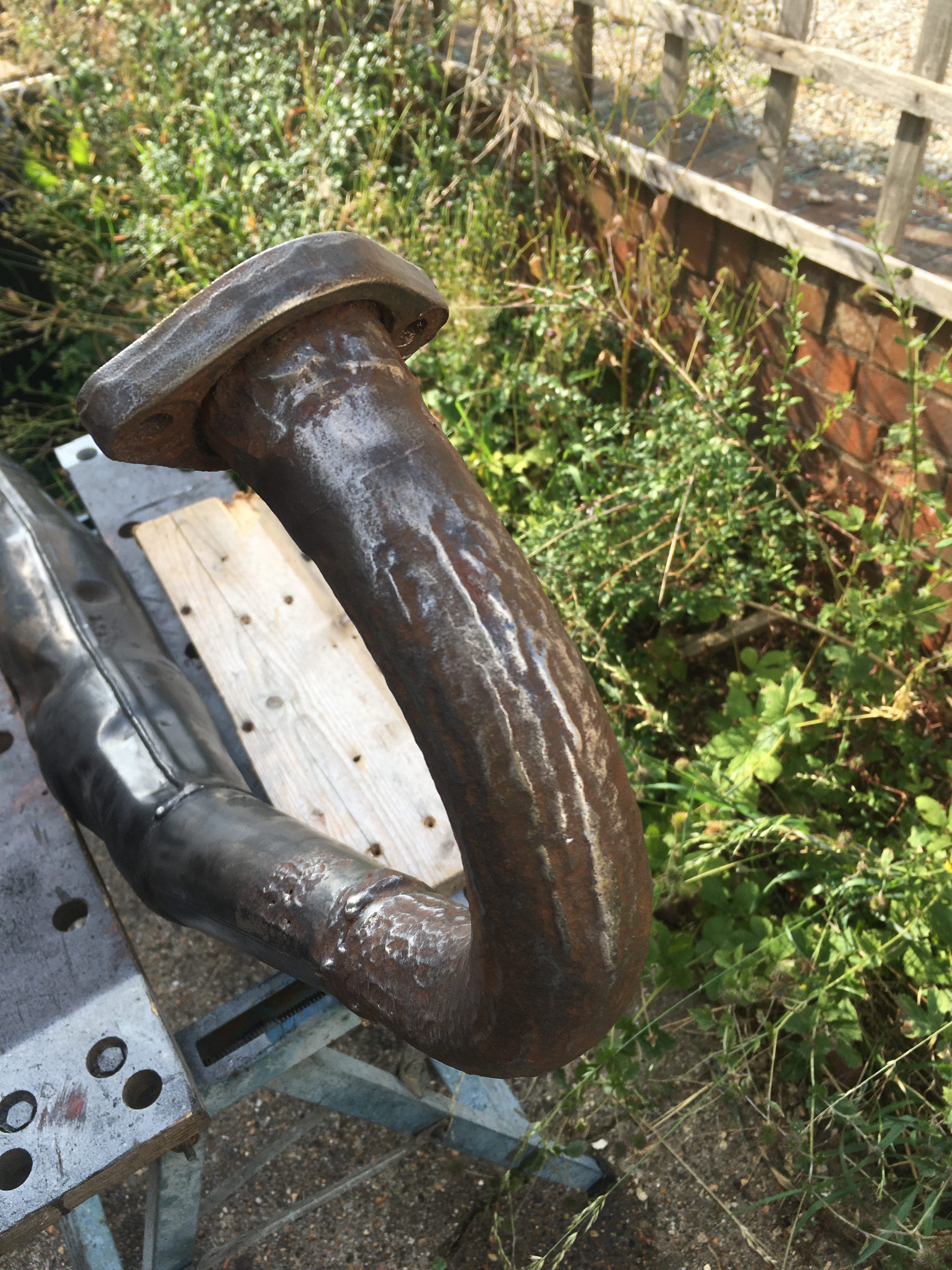
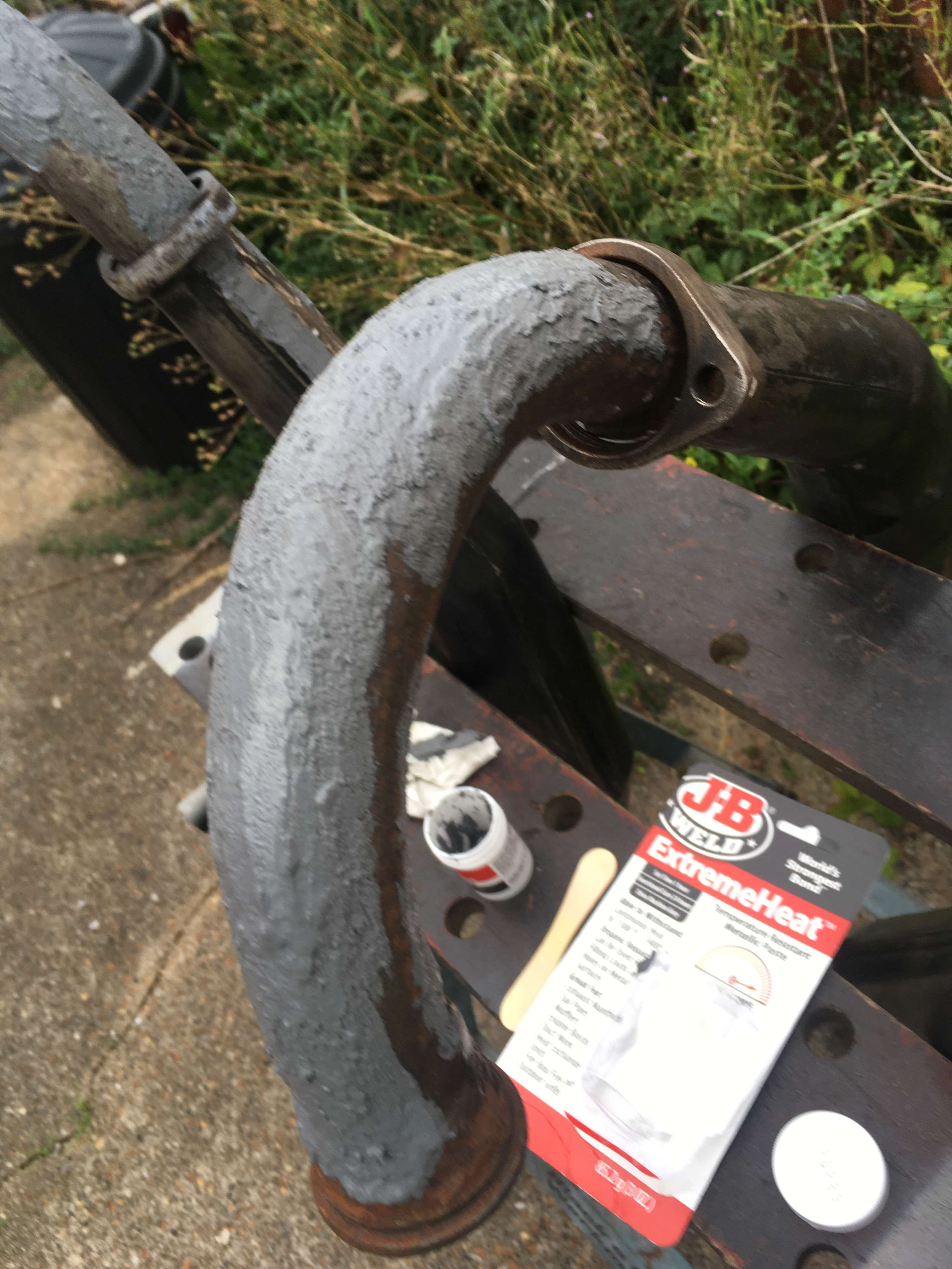
After allowing to cure for, as it turned out, 36 hours, I initially used a file, and then some 240 grade wet’n’dry to remove the excess filler.
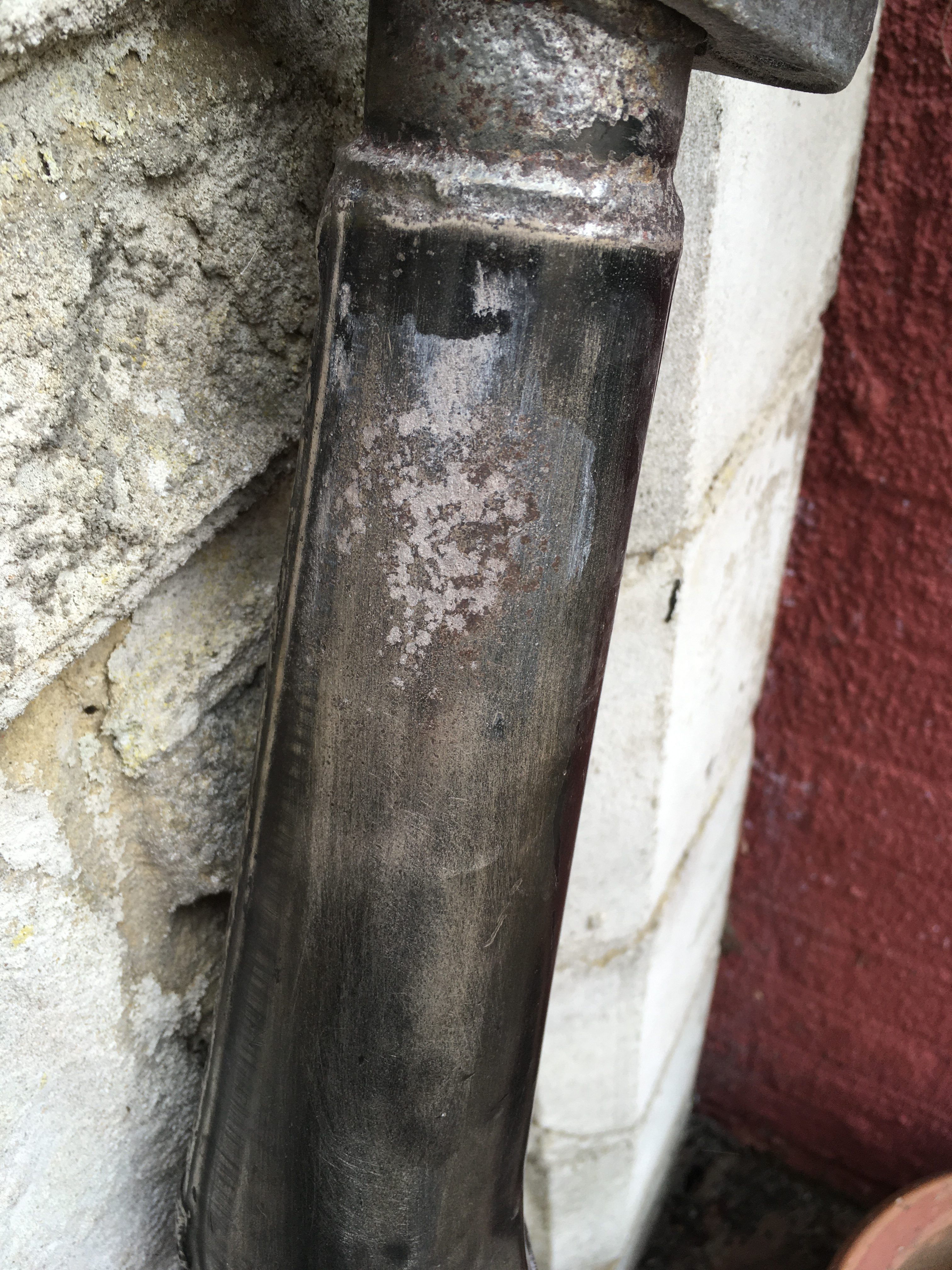
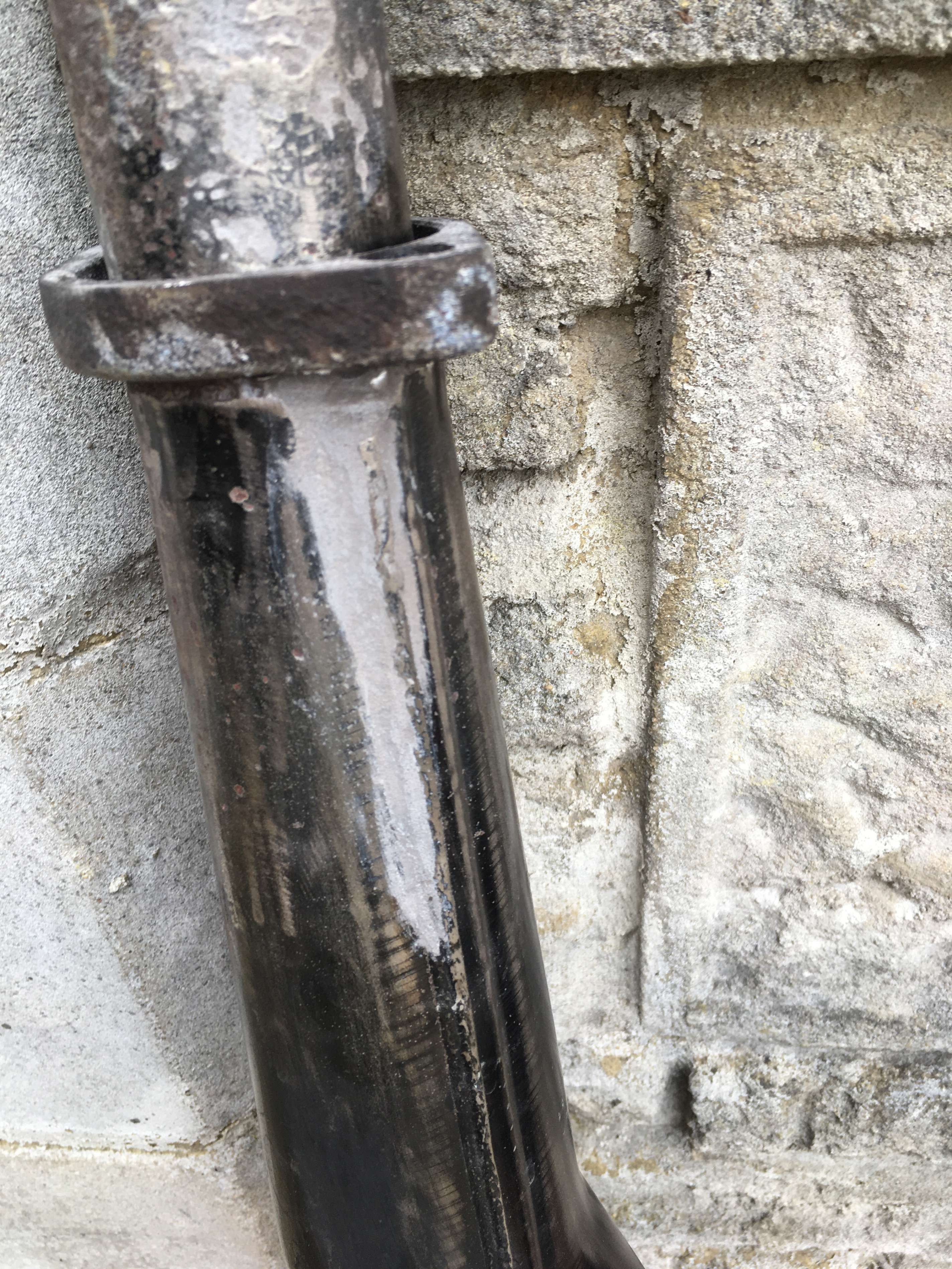
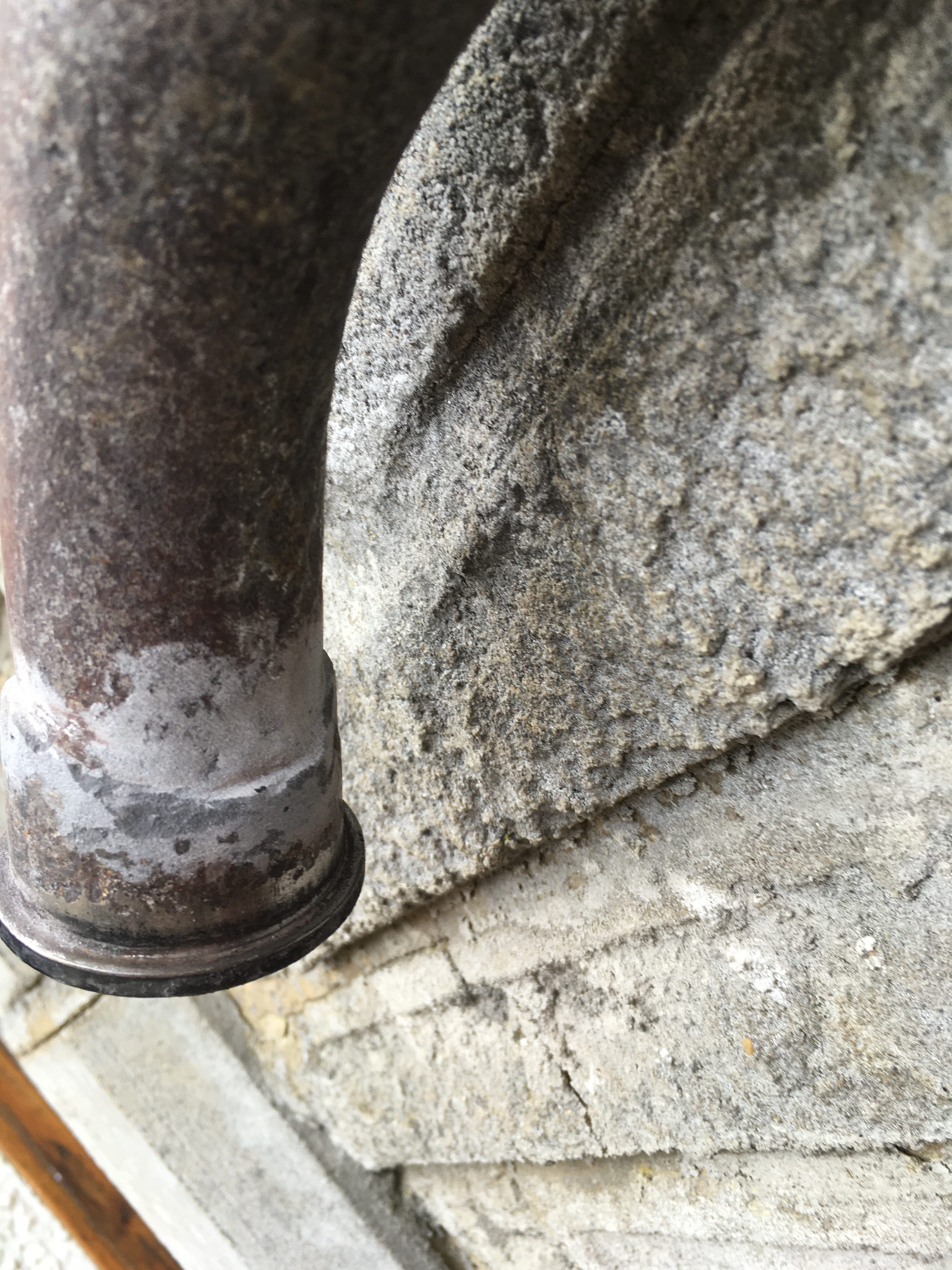
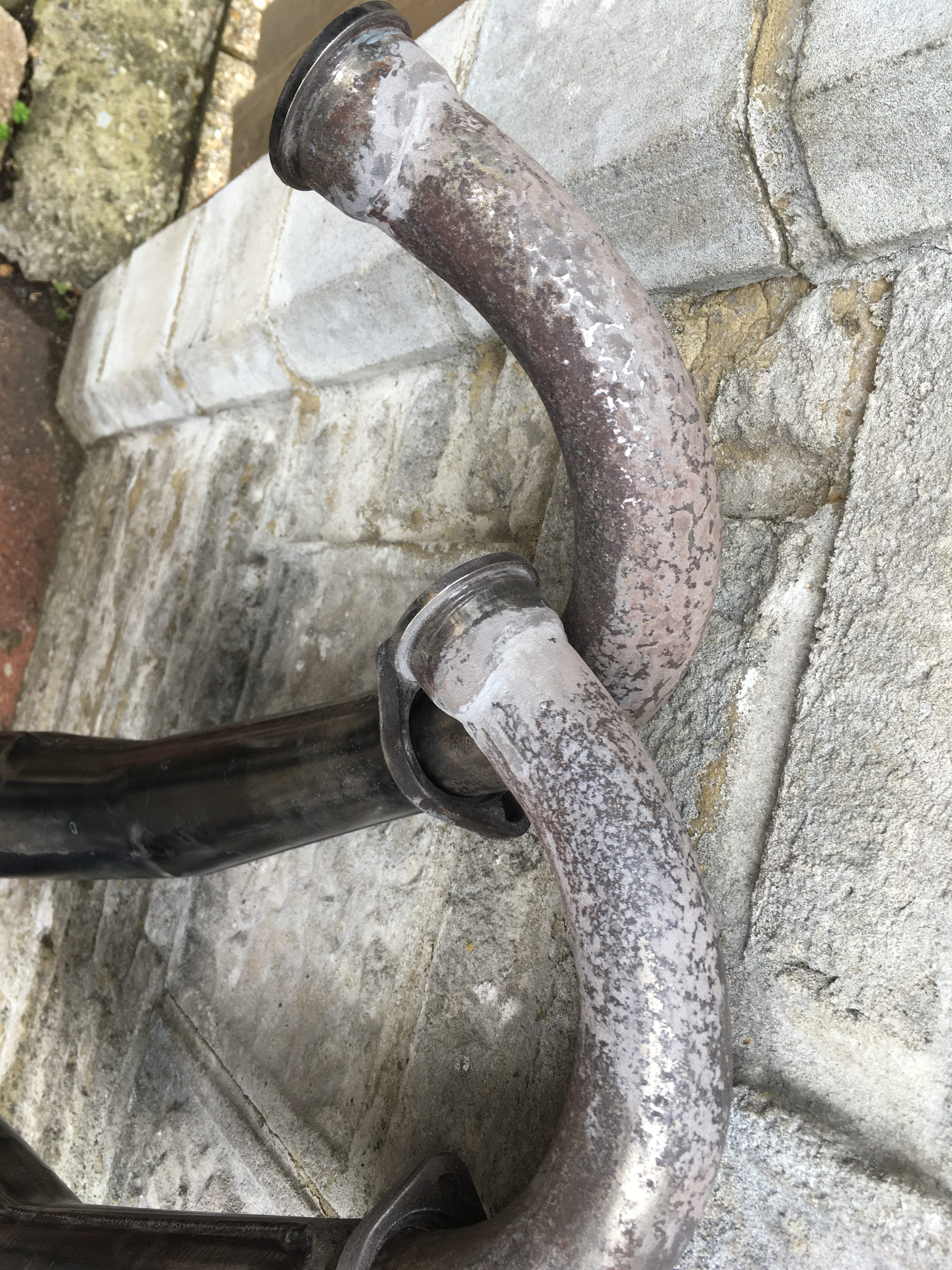
This all looks very promising for a first trial.
The downpipes look much better and the holes are filled.
While they could do with the application of another tub of the JB weld filler, I’m going to leave the filling there, and paint the pipes so they can be refitted to the bike and tested for the ability to continue stopping up the hole, and to see if the filler drops off of the rusted, and Ferric Phosphate areas over time.
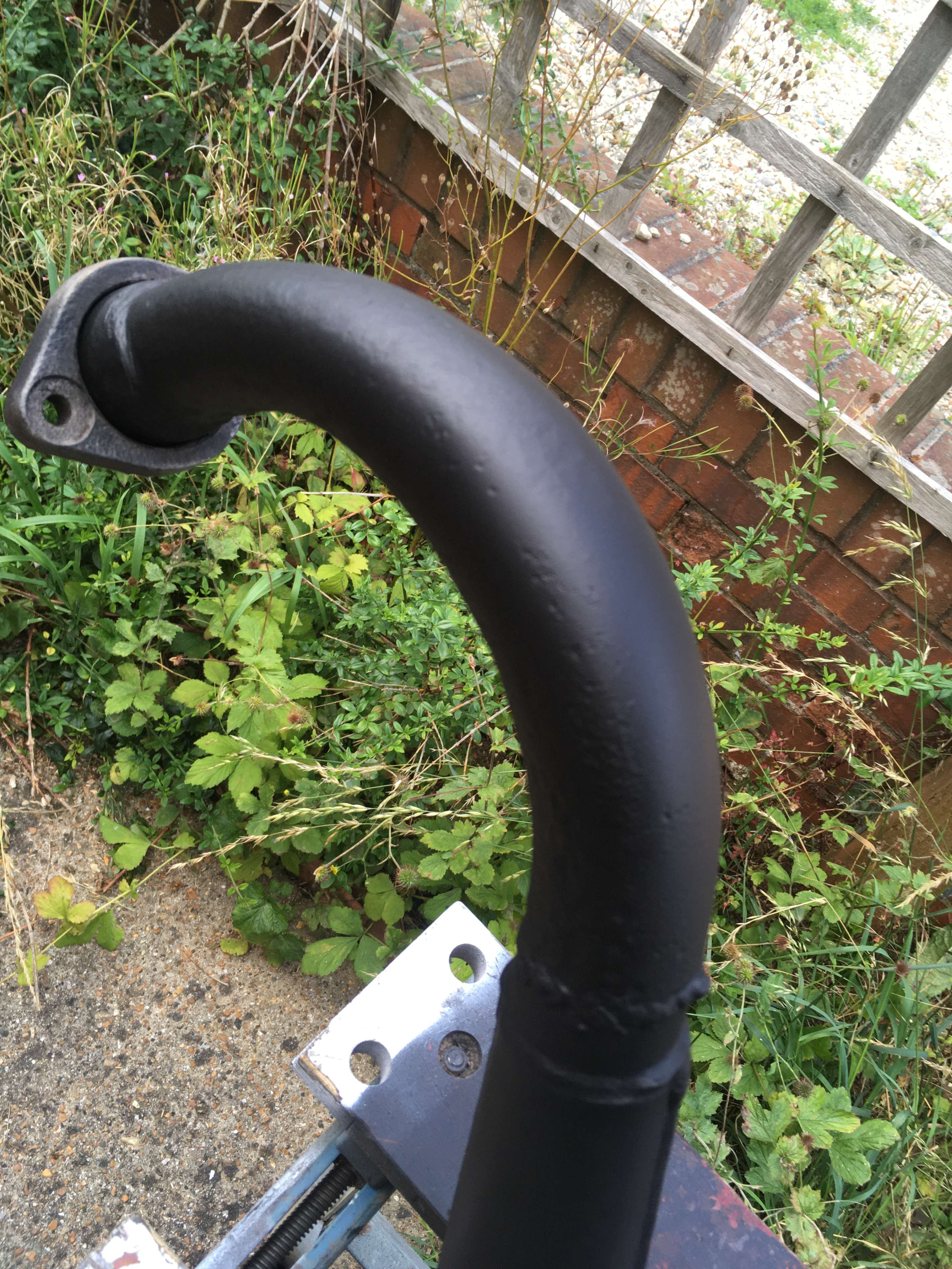
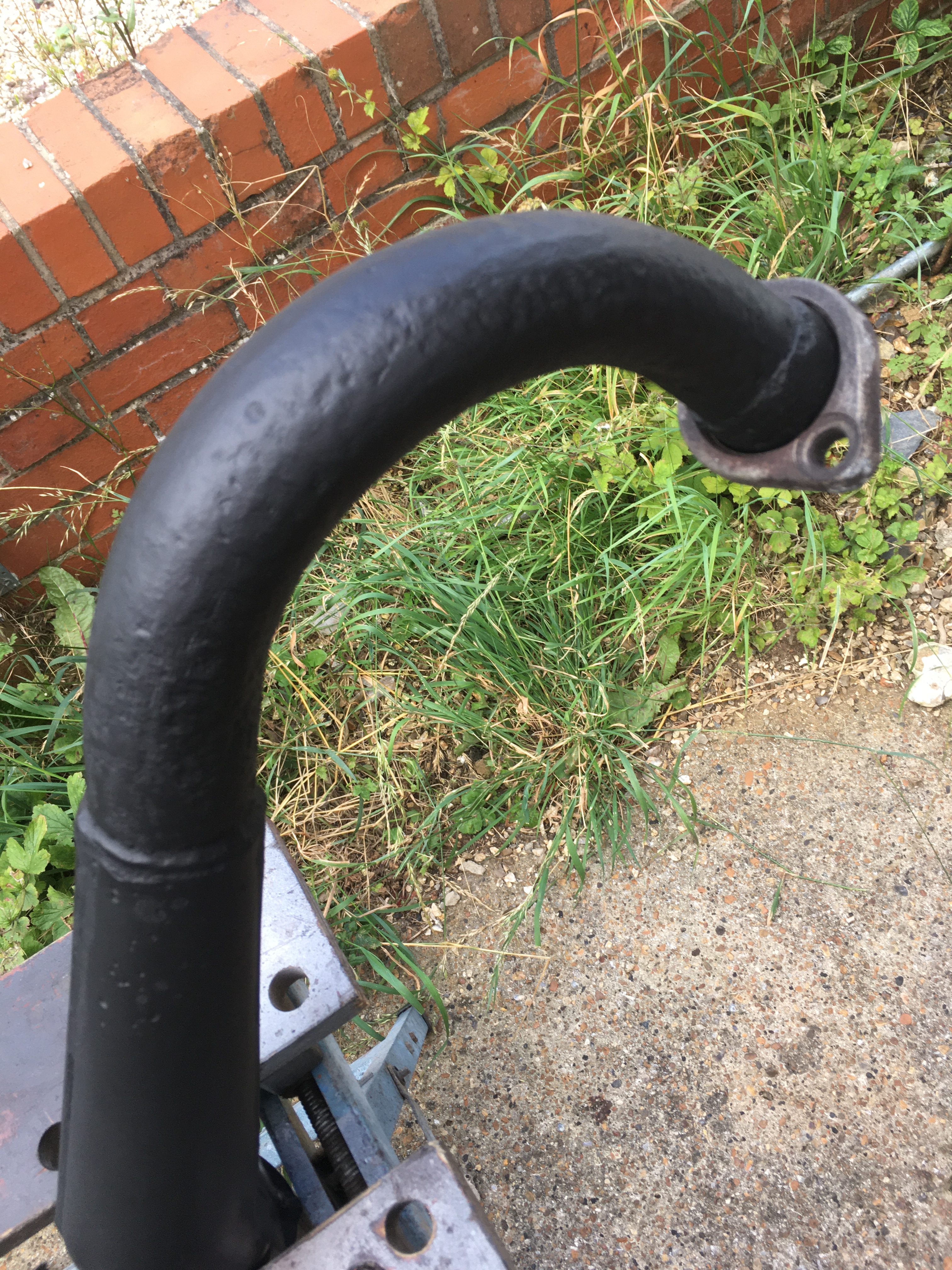
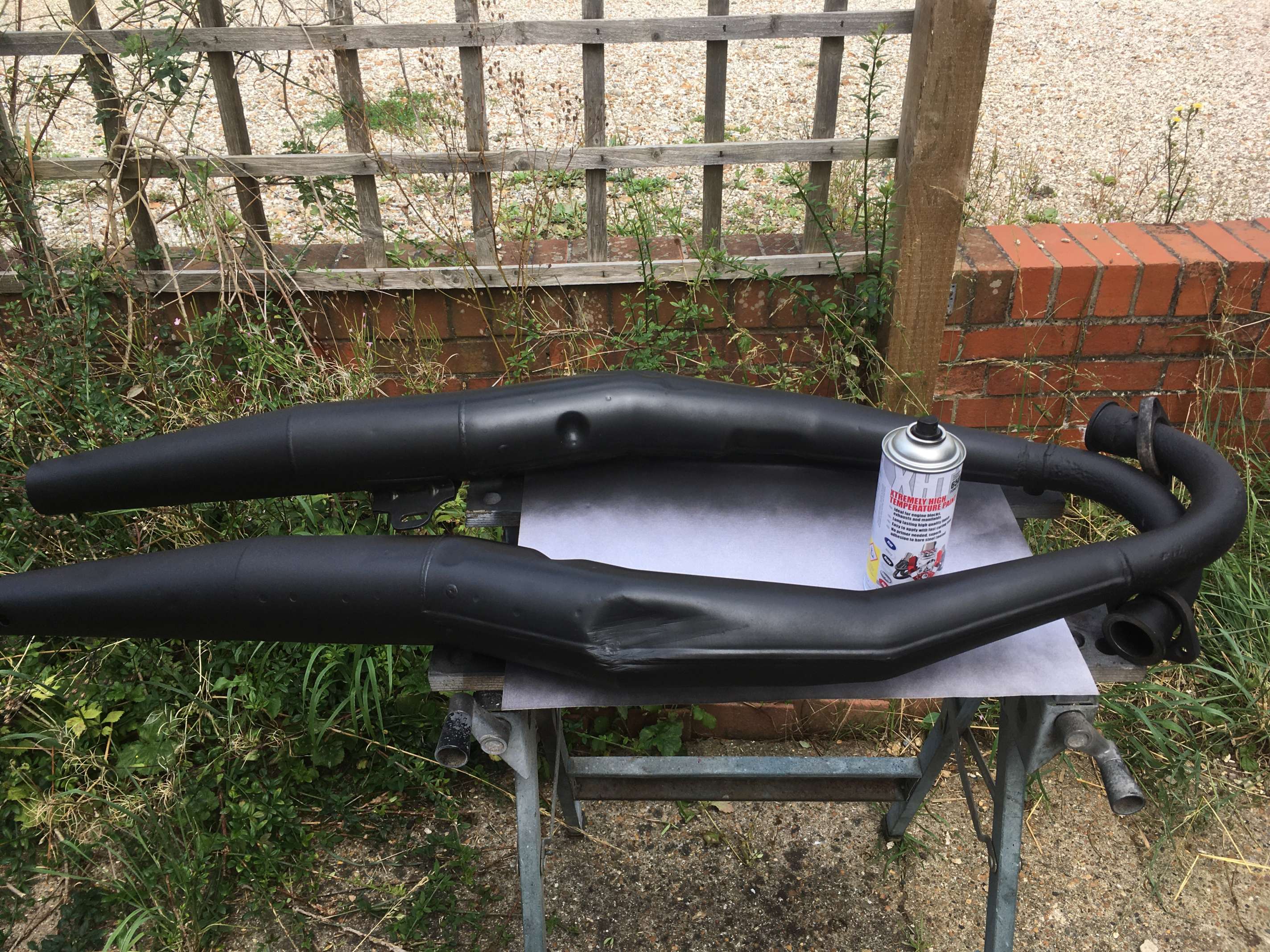
Back on my bike tomorrow.
Update September 2022
A year later and I’ve done less than 100 miles on the repaired 31K pipes fitted to my RD350LC.
The use of the JB weld Extreme Heat filler has worked very well in filling the pits in the downpipes.
The filling of the pinholes by the header on the LHS pipe has also survived OK, and formed a gastight seal… so far.
Using it to fill the big hole in the RHS downpipe has proved to be an abject failure however. The hole blew through almost straight away.

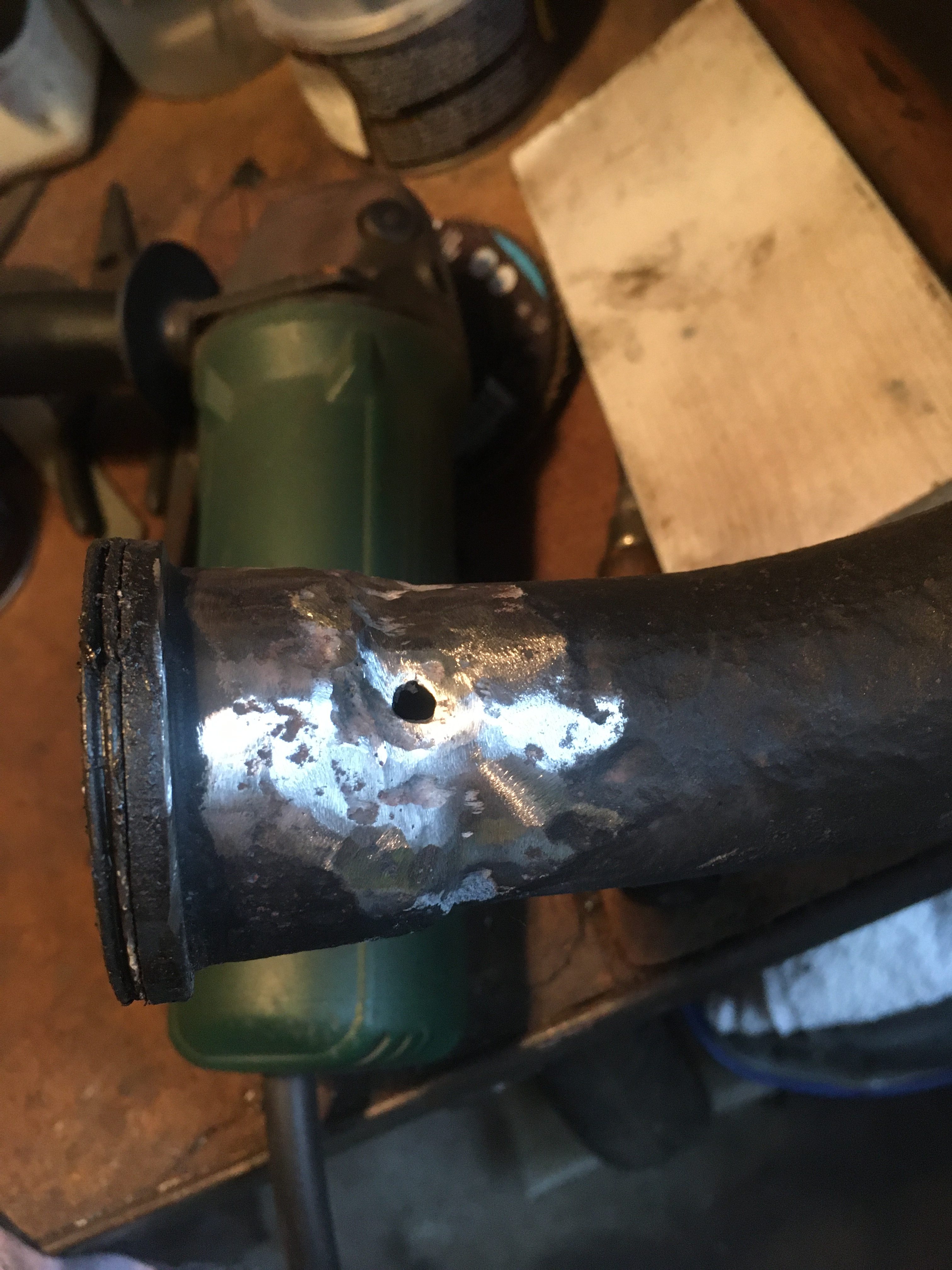
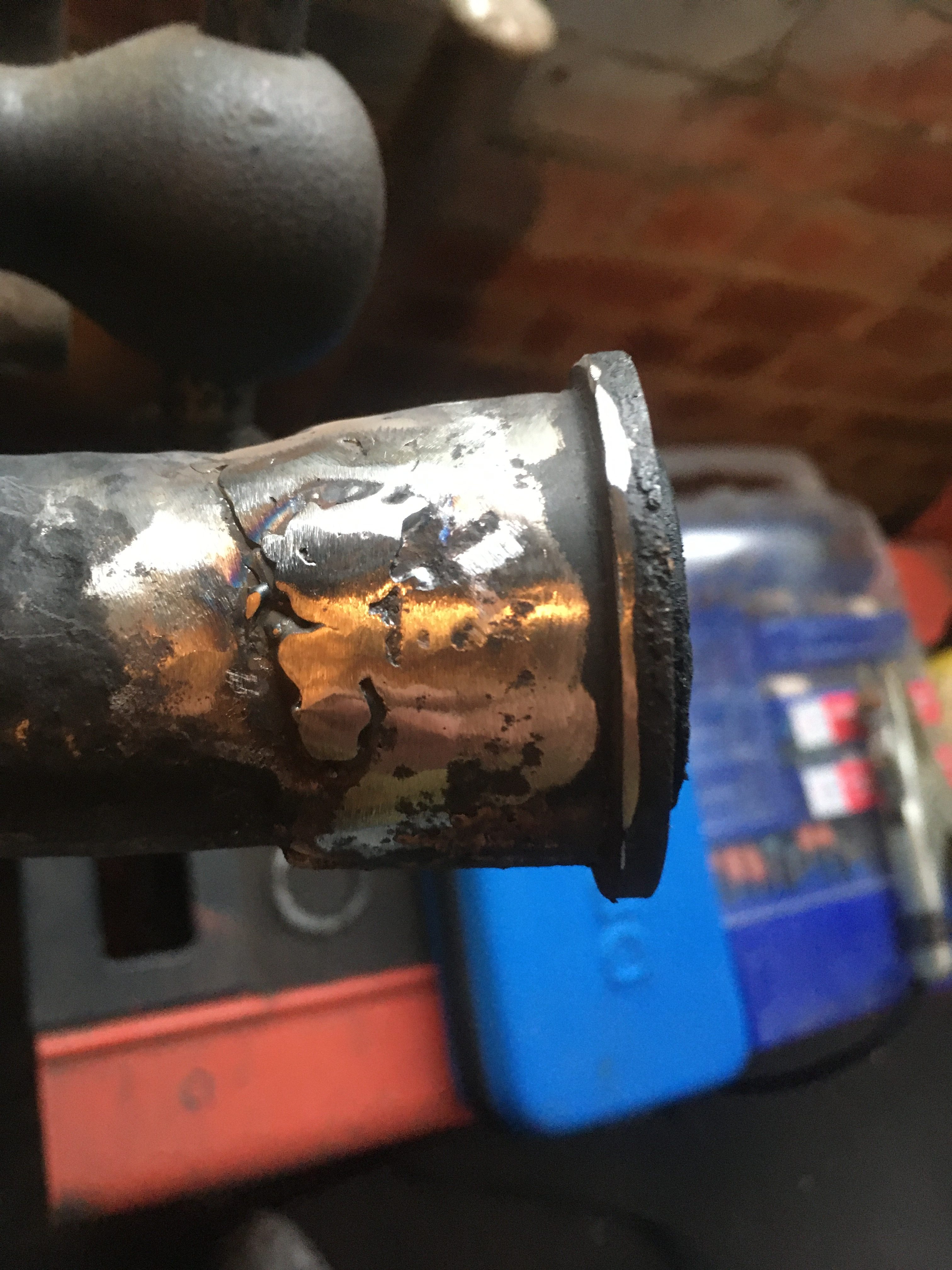
It was time to dust off the MIG and get welding.
First, grind back the JB weld and return the operating area to bare metal.
The JB weld is not “metallic” as I had expected, but much more like a more traditional bodyfiller with a chalky talc like consistency. I could have removed it with a fingernail.
I am a completely novice untrained welder, so my best hope was to fill the hole with “chicken shit” blobs, and grind it back.
I seem to have achieved this, but the proof will be in the refitting and riding through another winter.
As for the LC2 pipes… The JB weld which I used up on the heavily eroded downpipe on one side didn’t last the test of time just hanging up in the garage.
While I had removed as much rust as I could with a wire brush, the metal clearly needs to be forensically cleaned for the stuff to adhere.
i.e. It all flaked off.
I do want to try and reclaim the LC2 pipes however, so I identified 2 sited on the LHS pipe where holes had appeared, and welded patches on.
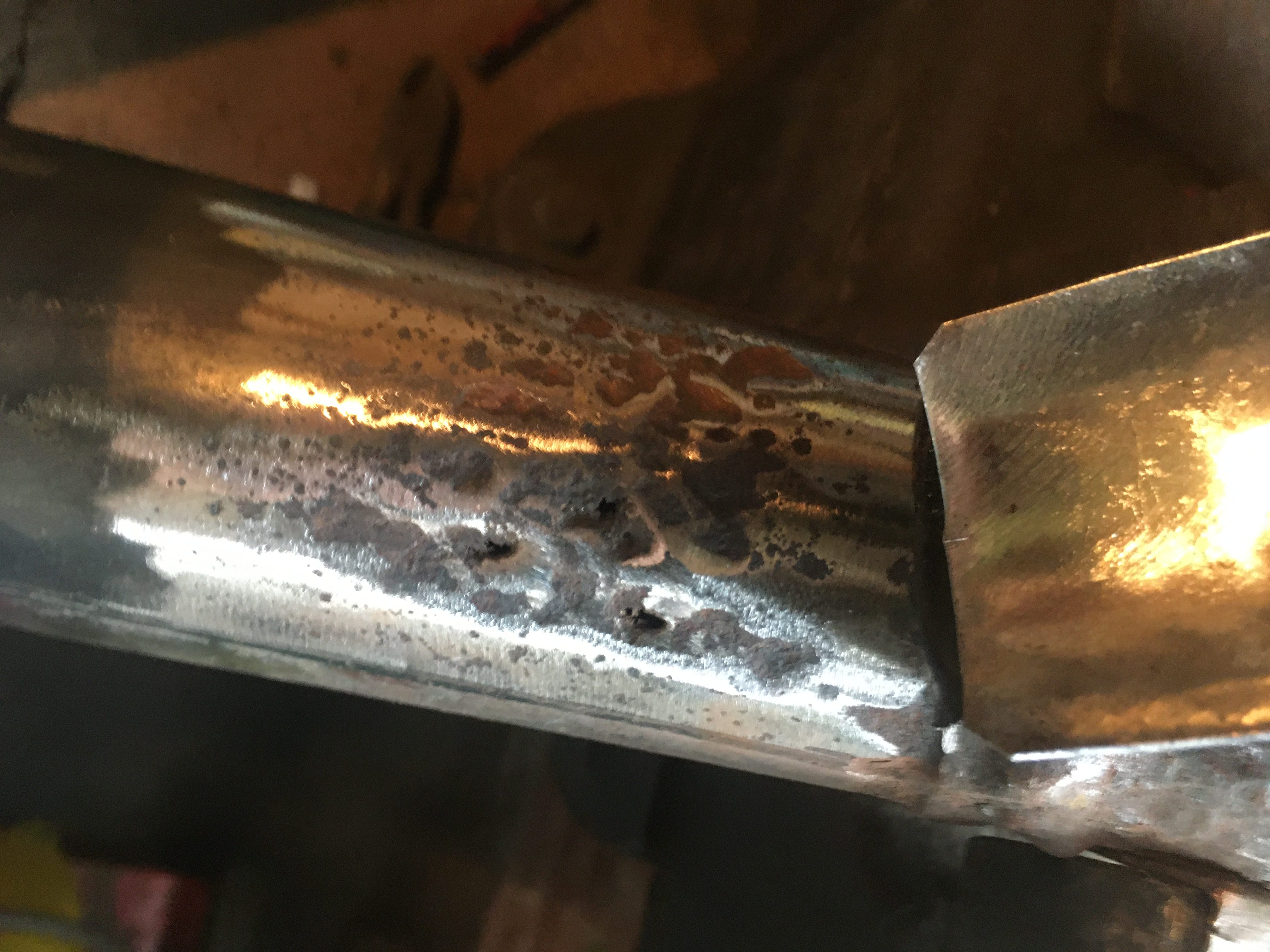
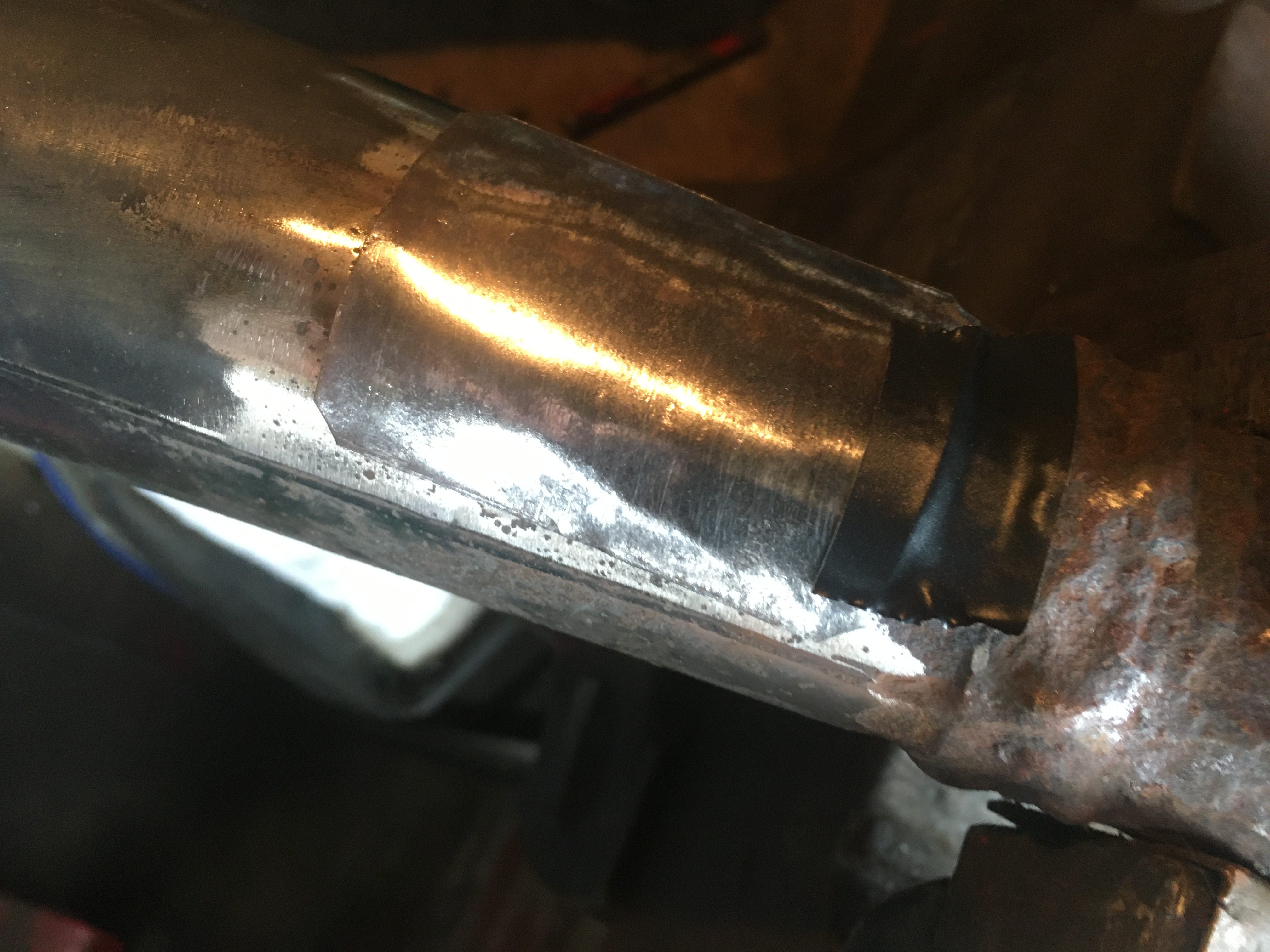
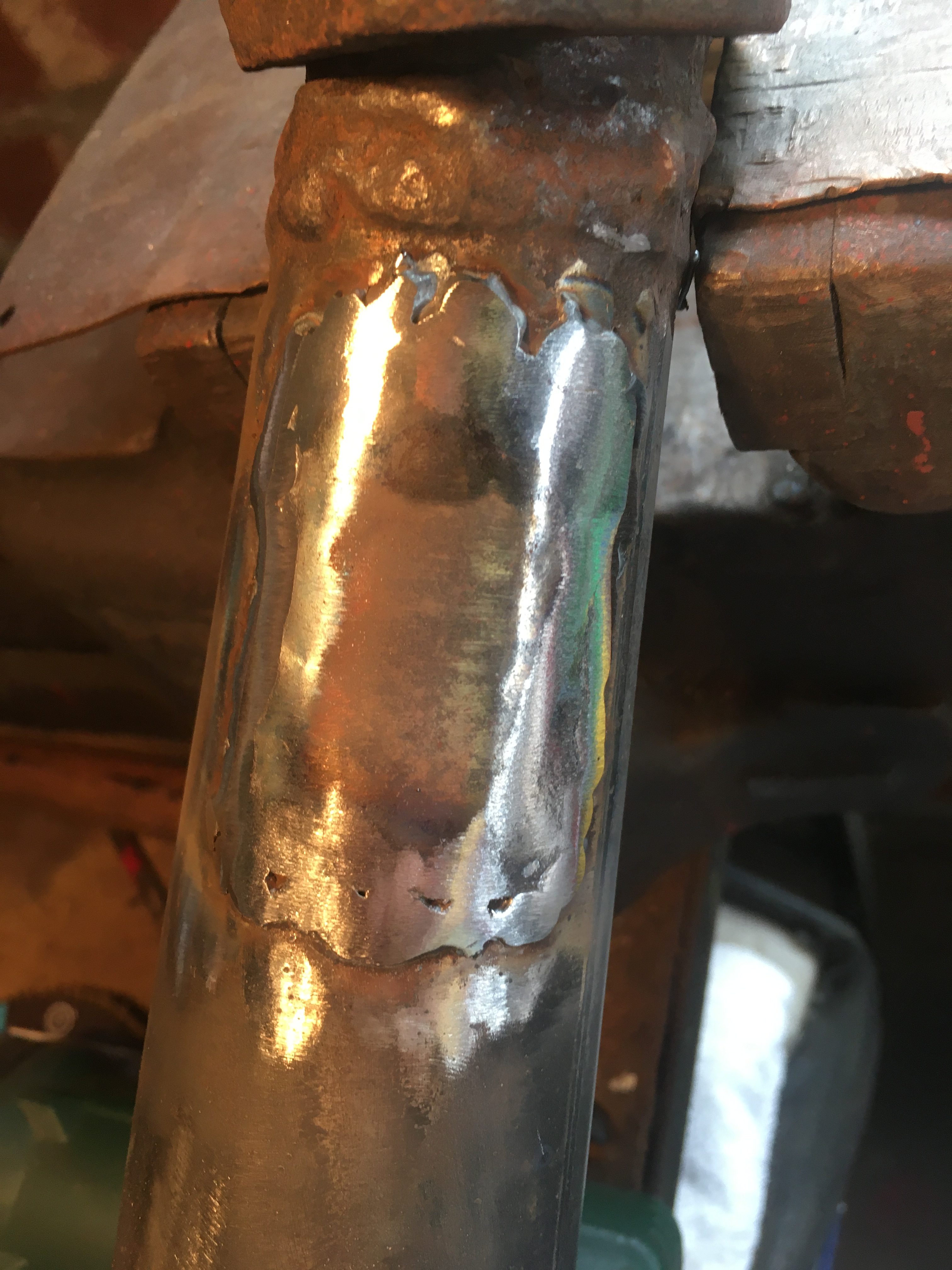
The bigger dents on both pipes I rubbed back to bare metal and filled with a more traditional bodyfiller. The damage is well back from the hot downpipes so I’m hoping that the “metal filler” I have selected will do the job.
This looks like a job which will be completed piecemeal over time, as I have no pressing need for these pipes at present and to a certain extent, the experiment is to see if such a poor pair of pipes can be reclaimed at all!
So in conclusion, JB weld Extreme Heat has it’s uses, but also has some limitations, and is not an alternative to welding for fixing large, pea sized holes in downtubes.