In May of 2019, I noticed that the frame was beginning to rust.
I had carefully left it in the garage for 4 years without noticing that the garage had a tendency to damp.
Resolving to start The Project, I moved stuff around in Garage to clear a space for working.
With all of the parts originally removed and dismantled in a big pile, I fastened the frame to a workmate bench with a tiedown, and started de-rusting it with a variety of powered and manual wire brushes.
Over the next 2 days, I completed the rust removal, and painted over the bare metal with the excellent Bonda Primer, a paint concoction which chemically bonds with, and changes the rust which is left on the metal underneath.
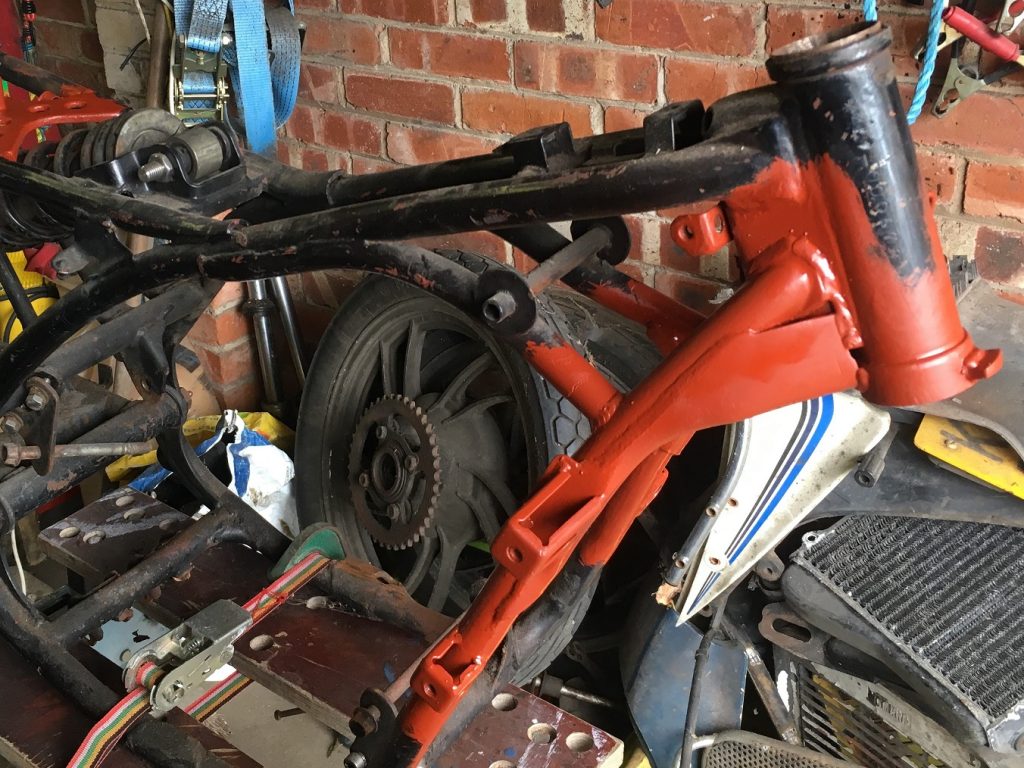
The following day, I continued with the obvious and necessary next steps.
The taper head races were, as expected, shot, so I set about removing them.
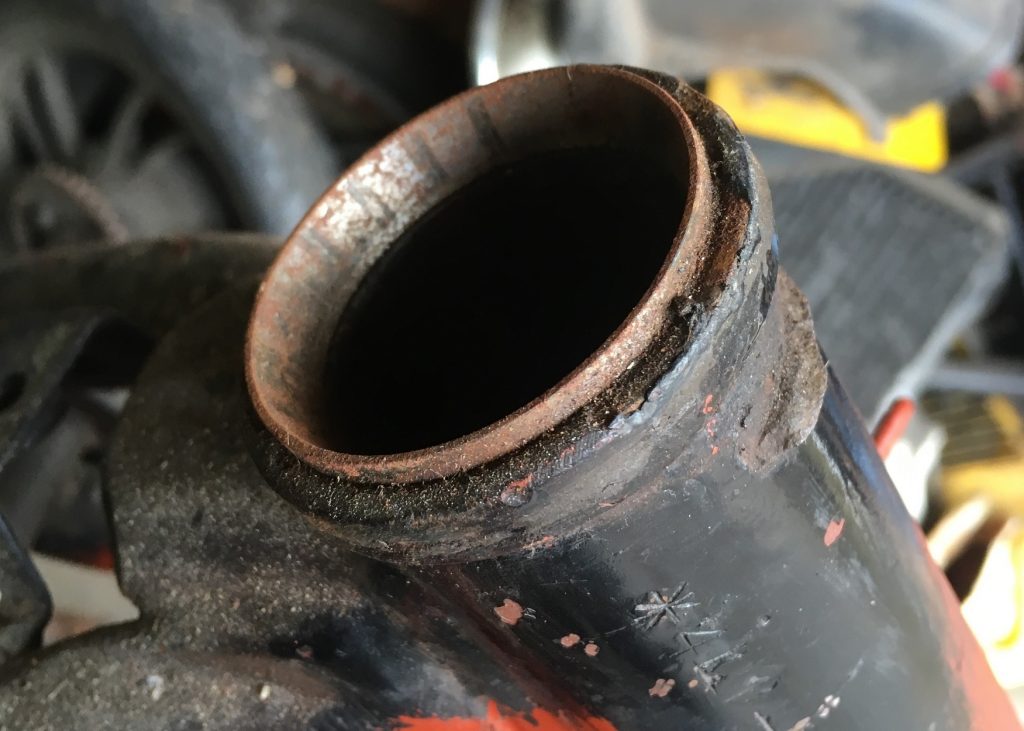
Normally, I would simply use a longish drift inserted in the headstock, and using a small hammer, knock out the race by resting the drift on the protruding part of the headrace.
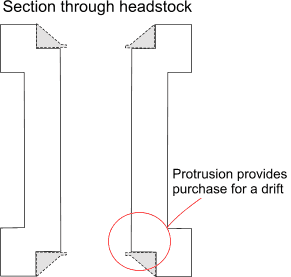
The problem was that these headraces had no protruding part to gain any purchase.
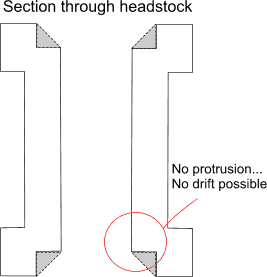
Lots of sites unearthed by Google suggest welding a steel bar to the bearing and then knocking it out.
However, either. My welding isn’t good enough or the taper races are not conducive to welding. The weld just breaks away from the bearing face.
Eventually, applying a bit of logic, I Dremmeled out some of the HEADSTOCK interior so I can get purchase on the bearing with a drift.
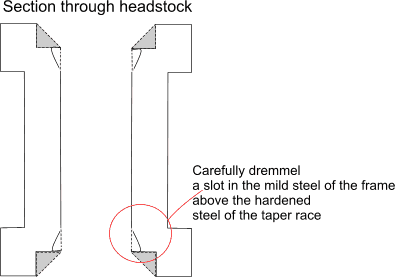
It Worked!
However, I had a safety failure, and forgot to wear my safety specs/goggles, and a pair of ordinary glasses provide scant protection from red hot showers of iron filings.
I got a metal splinter in my eye.
Some days, and a visit to the local eye hospital later, I could see again, but my enthusiasm for The Project had waned somewhat.
Rather than crack on with the nuts and bolts, I spent some time making a list of all the things I should be doing if I was so inclined…
- fit new headstock bearings and top/bottom yokes
- Remove swing arm
- check bushes
- Rub down rusty bits on swingarm and paint with bonda primer
- Refit swingarm
- Rebuild front forks
- Measure and select fork springs from the many I have available
- Buy some new fork oil of correct grade
- Find 250 barrels and head combination in decent condition in my vast pile of spares
- Select a pair of 250 exhaust pipes from the pile of rust and broken pipes in the corner of the garden shed.
- find a 250 oil pump
- find a pair of 250 carbouretters, (and the correct jets)
- Find/Buy a throttle cable
- Find/inspect/repair wiring loom
- Find/inspect/repair front brake caliper
- Fit forks, headlamp brackets, headlamp shell, clocks, handlebars, switches
- Replace where necessary
- Fit rear bracketry, mudguard, tailpiece and light.
- Fit wiring loom
All of this may seem a bit forward, but I have a big pile of LC spares built up over the past 30 years of owning one.
Additionally, this build won’t be concourse, nowhere near.
In fact, the first build won’t even have proper paint.
It’s just a mechanical build to prove we can get it through an MOT, and to identify all of the parts which will need replacing with new, once we get around to the final build.